During a talk organized by the Big 5 Global event in Dubai, we learn more about what it means to decarbonize steel and how the Emirates Steel Arkan enterprise is on a journey to net zero.
December 4-7, 2023—Leaders in the construction industry unite once again at the Big 5 Global event in Dubai, discussing important topics such as carbon-neutral concrete, data-driven district cooling optimization, decarbonizing steel, and more. The event organizers invited representatives from Emirates Steel Arakan to discuss the company’s journey to net zero emissions.
As the largest steel and building materials producer in the UAE, Emirates Steel Arakan holds a domestic market share of 60%. The company uses natural gas in its production with a manufacturing capacity of 3.5 MTPA of long steel products. The final products are exported to more than 70 countries worldwide including some in Europe.
“We know that decarbonization is expensive and takes time, it’s not a walk in the park,” said Fadl Mohamed, Strategic Partnerships, Decarbonization Leader at Emirates Steel Arakan.
The company has been “accelerating” the transition to a low-carbon economy to achieve the steel industry’s decarbonization goals, in line with the UAE’s Net-Zero by 2050 initiative.
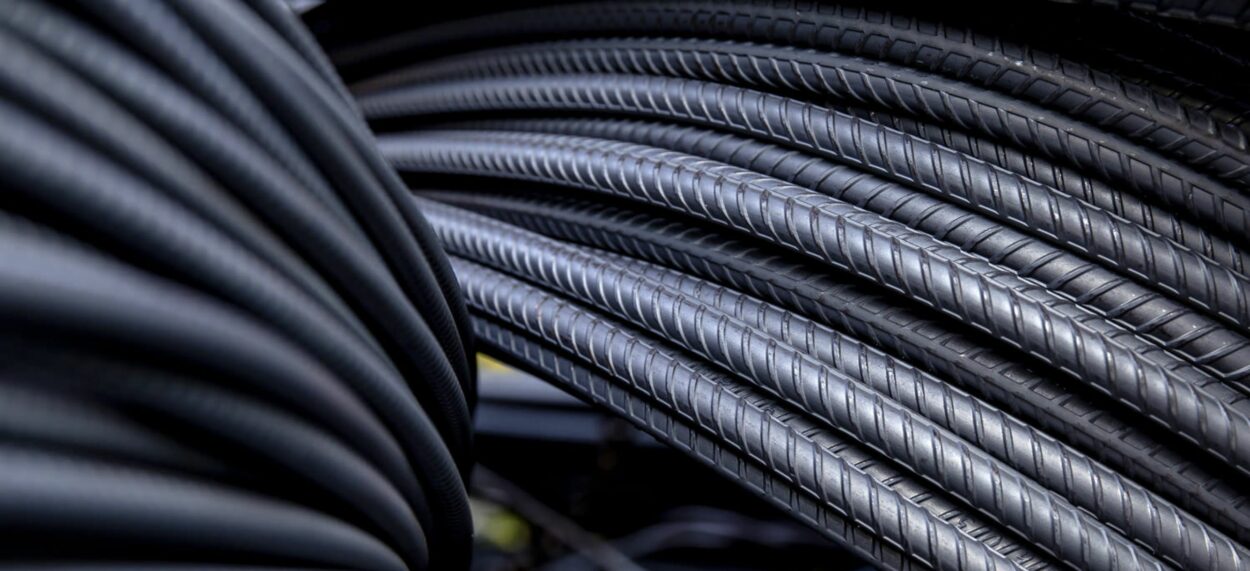
They currently produce 40% less carbon than their peers, driven by a range of decarbonization initiatives and spearheaded by the utilization of a carbon capture facility, and the use of scrap and clean energy in their production process.
The process begins with what they call “reduction production” which has three direct reduction plants with a capacity of 4.2 Mt, followed by steel making with three steel-making plants with a capacity of 3.6 Mt, then rolling with one heavy section mill, three rebar mills and one wire rod mill. Finally, the products are produced.
To reach this stage, they have invested in R&D in which they took the initiative to explore new materials and processes that have lower carbon emissions aiming to continuously improve the sustainability of their steel products. Then they leveraged an innovation process to launch the Rebar ES600, an innovative low-carbon rebar that aims to reduce steel consumption in construction by 18-24%.
“This product has been successfully used in two prestigious projects in Dubai,” said Mohamed.
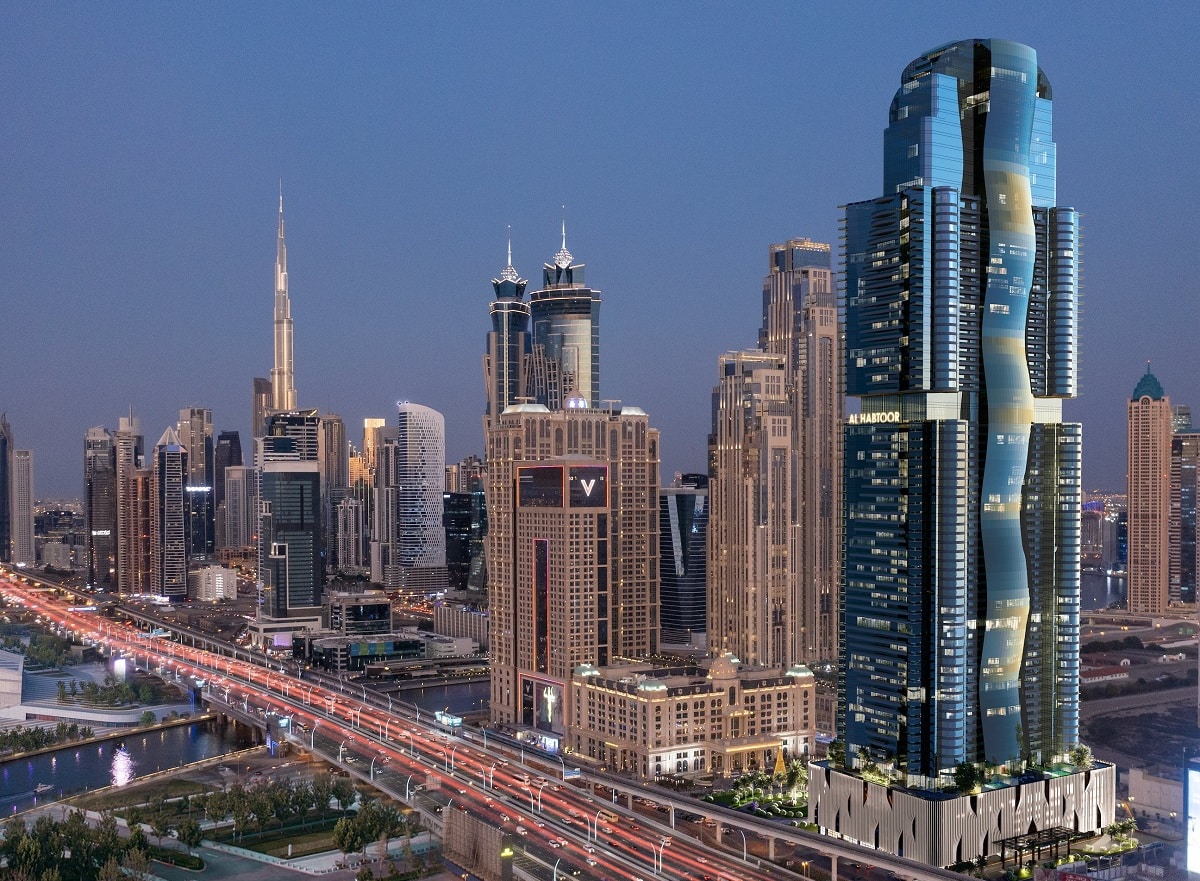
The Rebar ES600 is a high-tensile rebar that is produced by Emirates Steel and gives significant savings in construction. The rebar is also used in producing wire rods and coils.
Mohamed emphasized the importance of digitalization in the process. According to him, the company has implemented a comprehensive monitoring system to closely track its production processes and emissions.
“How can I prove to you as customers that something from outside the company is being done in a good manner? When we talk about digitizations, it’s about how to follow the project from the mining process to the shipment or the usage of the project. When we do that, we can follow the emissions, where they have been established, and we can certify them to say they are low carbon,” he explained.
Steel contributes about 8% of global carbon emissions, with an increasing focus on the target to achieve net zero, and the target to achieve a 50-52% reduction in greenhouse gasses by 2030, steel decarbonization is gaining significance.
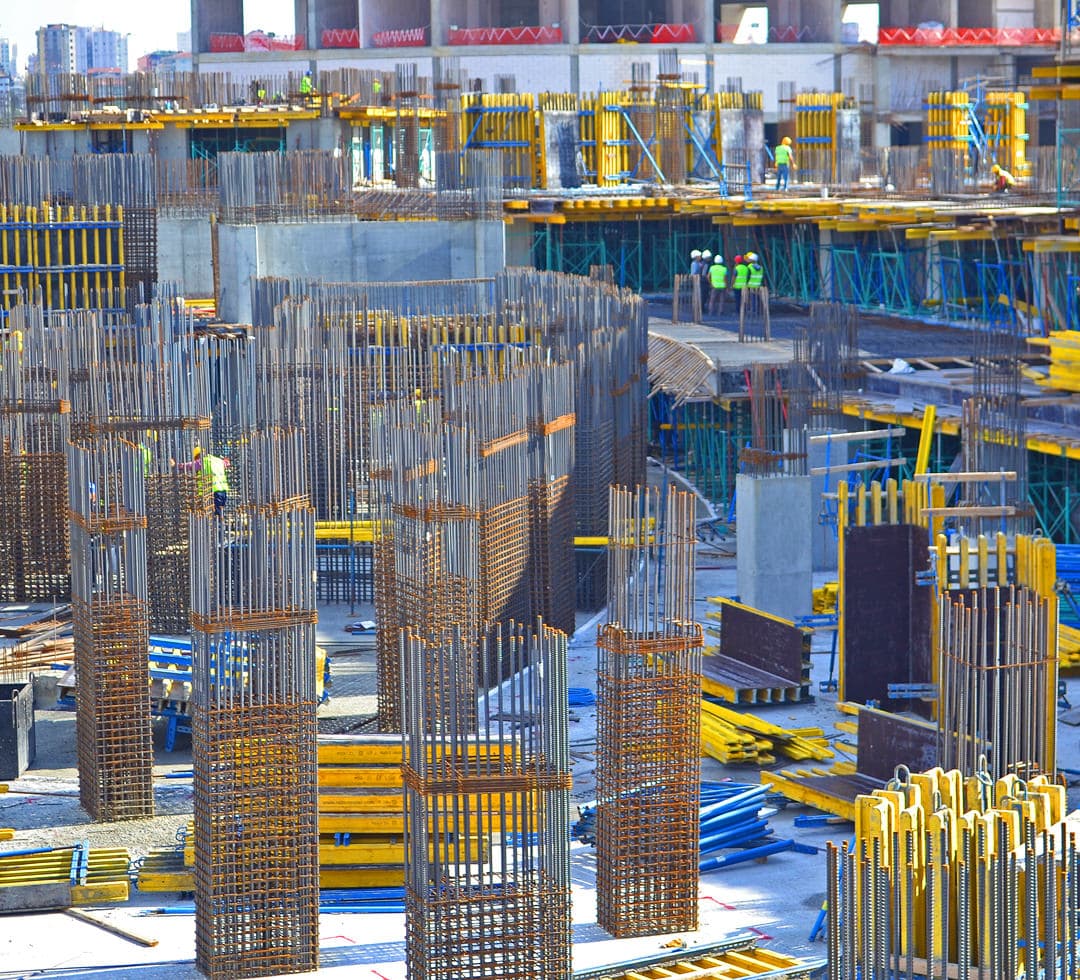
Therefore, steelmakers can either invest in fixed assets and incur additional costs to reduce their carbon footprint or pay carbon taxes to offset their carbon footprint.
“We understood what our emissions are then we put them into boxes which include carbon capture, clean electricity, increased scrap charge, energy efficiency and the most important is digitalization,” explained Mohamed.
Green steel comes with various advantages including economic, emissions, budgetary, electrical, and also demographic. The company collaborated with ADNOC and Masdar to create a CO2 capturing project and other projects such as an electrolyzer for hydrogen production to ensure that they can reduce the steel industry’s carbon footprint in the future.
Decarbonizing steel, however, is challenging due to the lack of infrastructure, electricity, and hydrogen’s existence which could have a high impact on decarbonizing steel. Hydrogen, which is an alternative to fossil fuel, is expensive and has not been mass-produced yet. Mohamed said that when hydrogen becomes available, steel will be completely decarbonized.
“The most important challenge remains to be the rules and regulations, how many things should I sign to get the process done,” explained Mohamed.