Several startups have been innovating the construction industry with exceptional wood materials: TimberRoc, a wood concrete, Blokiwood, a modular block system, and Brikawood, a wood block system that fits together without nails, screws or glue.
In France, the use of wood materials in construction offers numerous opportunities to promote sustainability and the valorization of natural resources. Wood materials such as glued-laminated timber (GLT), cross-laminated timber (CLT), oriented strand board (OSB), medium-density fiberboard (MDF), and other wood-based products provide an ecological and sustainable alternative to non-ecological materials.
Currently, the wood industry strives to comply with environmental standards and promote sustainable practices, notably through certifications like PEFC and FSC, which ensure responsible sourcing of wood. However, there is still untapped potential to maximize the use of local wood and reduce dependence on imports. It is important to examine the market and gain a better understanding of the origin of by-products used in construction in France. The share of French resources (processed) in final consumption is 59%, with the majority still coming from resinous woods. La Fabrique à Bois provides tables with technical characteristics of deciduous (hardwood) and coniferous (softwood) trees to facilitate wood selection for construction projects.
In recent years, companies and startups have been working on wood material innovations to further advance the sector. Here are a few examples of what can be found in the wood industry in France today.
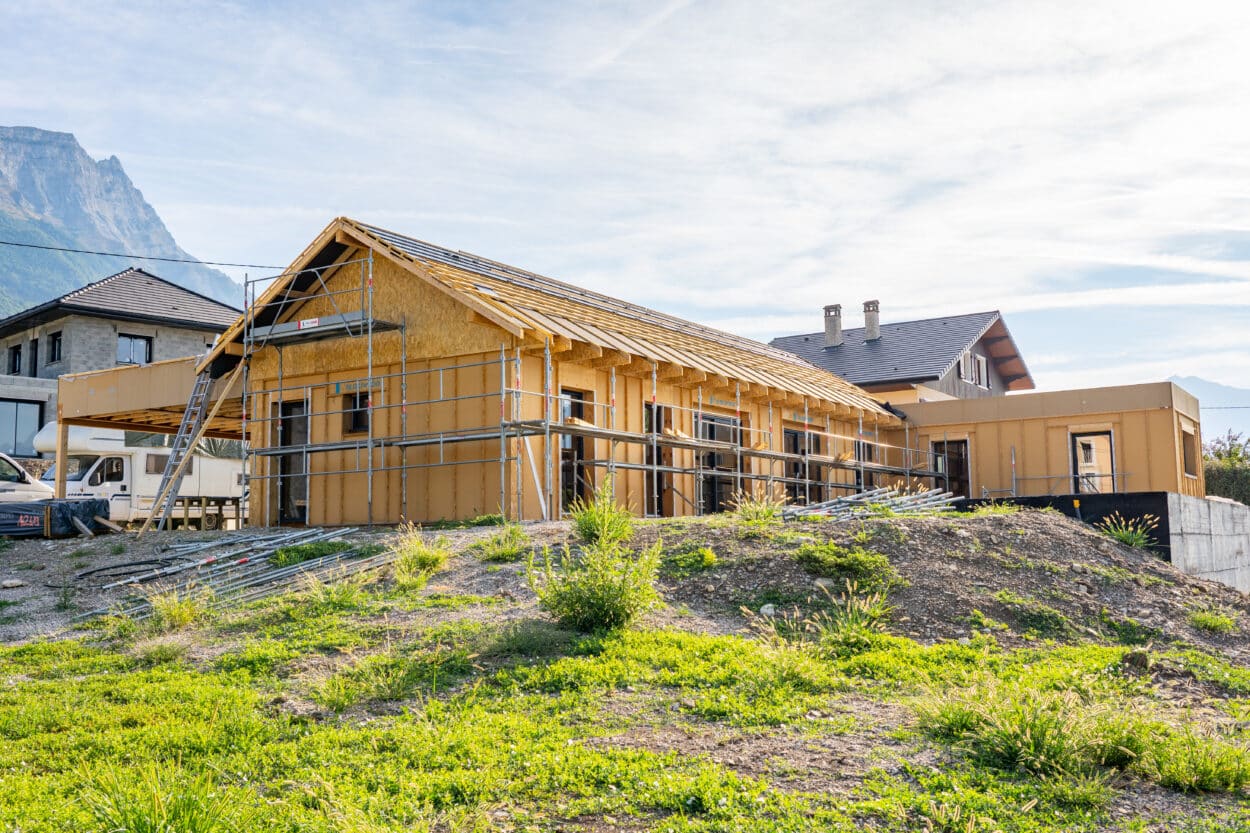
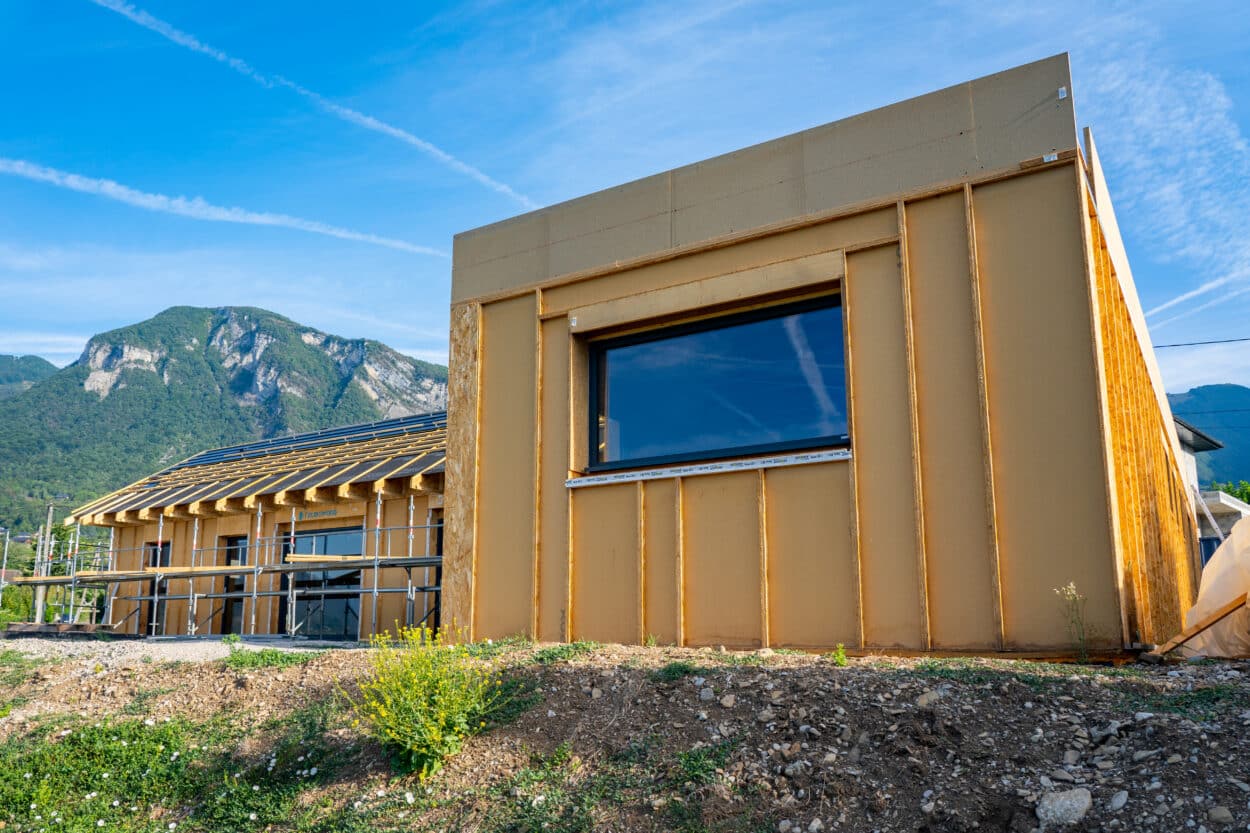

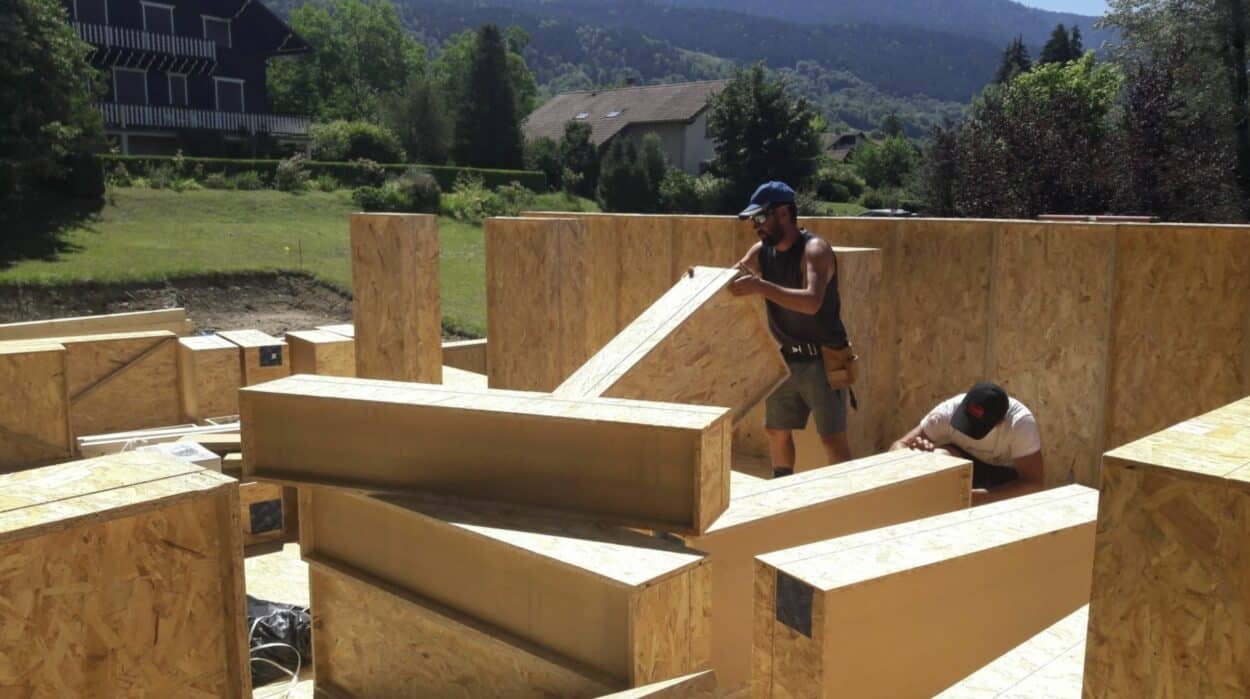
Blokiwood: 100% French Prefabricated Modular Blocks
Blokiwood offers modular block solutions for building professionals, including contractors, general contractors and artisans. The prefabricated modular wooden blocks reduce construction timeframes and simplify the building process. They come with a ready-to-use structural package to complete the entire structure. The blocks can be used for the walls, slabs, floors and roofing elements.
The advantages of Blokiwood include exceptional thermal comfort, ensuring warmth in the winter and coolness in the summer. Additionally, it promotes energy efficiency, enabling the construction of low-energy consumption homes. Moreover, the implementation of Blokiwood solutions is rapid, with projects often completed within a span of just 6 months. Furthermore, Blokiwood is proud to offer solutions that are 100% bio-based, contributing to sustainable construction practices. Blokiwood boxes allow for the creation of walls in any shape, accommodating a wide range of architectural preferences and supporting various types of finishes. These modular blocks, now featuring the Solar Impulse label, have a wooden structure with advanced cellulose wadding insulation, ensuring exceptional thermal performance.
Regarding roofing solutions, Blokiwood offers a variety of options, including flat roofs, traditional roofs and trussed roofs. For intermediate floors, Blokiwood presents two solutions: pre-cut I-beam floors and glued-laminated floors. The pre-cut I-beam floor provides a load-bearing structure composed of pre-cut I-beams and a lightweight pre-cut floor, eliminating the common issue of creaking noises and ensuring stability. On the other hand, the glued-laminated floor offers a visible underside and features pre-cut glued-laminated slabs that provide excellent sound insulation comparable to that of a concrete slab, while also allowing for an exposed bottom.
Blokiwood’s Posi-beam floor is another innovative solution, combining wooden beams with metal webbing to create a lightweight and rigid structure. This solution allows for extended spans of up to 14 meters without the need for intermediate supports, facilitating the installation of ventilation ducts and pipes without the requirement for additional drilling.
Brikawood: No Nails, Screws or Glue
Brikawood offers a system of wooden bricks that can be assembled without the need for nails, screws or glue, providing a more comfortable and energy-efficient living environment. The wooden brick construction system has undergone extensive research and development, resulting in 11 patents and approval from the CRITT Bois. Brikawood’s wooden bricks are proudly designed and manufactured in France, using high-quality Class 3 Douglas heartwood sourced from local FSC-certified forests, for its natural rot-resistant properties. While the company was launched in 2009, it wasn’t until 2015 the creators opened a production studio and began working on the first wood bricks. The following year, the studio produced two house kits per month. This year, Brikawood received the “maison zéro carbone” award and is recognized as an energy-positive building.
The Brikawood system consists of four elements: two side flanges and two transverse spacers, which are cleverly assembled using interlocking dovetail joints. This method ensures the structural integrity and dimensional stability of the wooden brick construction. With the Brikawood system, there is no need for additional cladding, rain screens, or vapor barriers. The simplicity of the system and its specific design features streamline the construction process, ensuring optimal performance and water resistance for various building types.
Brikawood’s wooden brick construction is adaptable to different architectural needs, whether it be for a passive house kit or a customized project developed with an architect. The load-bearing walls created with Brikawood’s wooden bricks are not only thermally efficient but also breathable, offering a healthier living environment. These walls are finished both internally and externally, providing a complete and aesthetically pleasing solution. Brikawood houses are made of 70% French-sourced Douglas wood, certified by PEFC and FSC, guaranteeing a sustainable and eco-friendly construction method. The low thermal mass of wood contributes to excellent thermal comfort, and studies have shown additional physiological benefits, such as reduced heart rate and blood pressure, promoting overall well-being.
TimberRoc: Wood-based Concrete Material
CCB Greentech (Carbon Capture Buildings) created TimberRoc, a revolutionary wood-based concrete material that offers a sustainable solution for construction projects. With TimberRoc, buildings can significantly reduce their environmental impact by 20 to 50% compared to traditional construction methods. TimberRoc’s unique composition enables the off-site fabrication of load-bearing walls and precast slabs with a negative carbon footprint. By utilizing a blend of water, wood aggregates sourced from certified French forestry operators (PEFC certified), and cement for strength and durability, TimberRoc delivers exceptional performance.
The prefabricated walls and floors made from TimberRoc are specifically designed to meet the requirements of low-energy and passive buildings, in accordance with the new environmental regulation RE2020. These structures offer outstanding quality, durability, and enhanced living comfort.
With an impressive 80% volume of wood additives, TimberRoc achieves an exceptional carbon footprint. The entire wood additive is utilized, ensuring zero waste and attaining the “Biosourced Building” label, which signifies between 100 and 200 kg of bio-sourced materials per square meter of floor area. Moreover, TimberRoc wood-based concrete is “breathable,” allowing for vapor diffusion and maintaining healthy humidity levels within the walls. This feature ensures a regulated and comfortable indoor environment, contributing to the building’s energy efficiency throughout all seasons.
TimberRoc offers not only sustainable construction but also exceptional thermal performance. Its distributed thermal insulation eliminates thermal bridges, while the material’s high thermal inertia results in a thermal phase shift exceeding 17 hours in a 30 cm thickness, with a damping rate surpassing 96%. With TimberRoc, CCB Greentech paves the way for a greener, more sustainable future in the construction industry.
VIDEO: You can select subtitles, then have the subtitles automatically translated into the language of your choice.
Coming Soon: Woodoo and LVL 100% French
French startup Woodoo is developing a number of wood-based products. While it’s too early to talk about their products in detail, we’re excited to see them reach the market. One of the products, Slim, is see-through and touch-sensitive. It’s specifically for smart surfaces. Flow is meant to be wood you can wear and will impact the textile industry, while Solid is wood as strong as steel for high, fast, dense buildings.
As we wait for more information on pioneering emissions-free building materials and processes from Woodoo, we can expect the first LVL 100% French by Le Groupe Thébault to arrive in 2025. The group presented the creation of the first production unit for Lamibois beams and panels, or LVL (Laminated Veneer Lumber), at the end of April this year. Although new to the French market, LVL has already proved its worth in the construction world, thanks in particular to its material yield and mechanical properties.
As part of the decarbonization component of the France 2030 plan, the project will receive €17 million from the French government and €3.3 million from local authorities and public bodies. This investment will be used to create a new factory in the Massif-central region where it will use a local species: Pectiné fir. The excellent mechanical qualities of this species convinced management to choose it for the industrialization of Lamibois. The new factory will be the THEBAULT Group’s 4th to be awarded the BOIS DE FRANCE label.
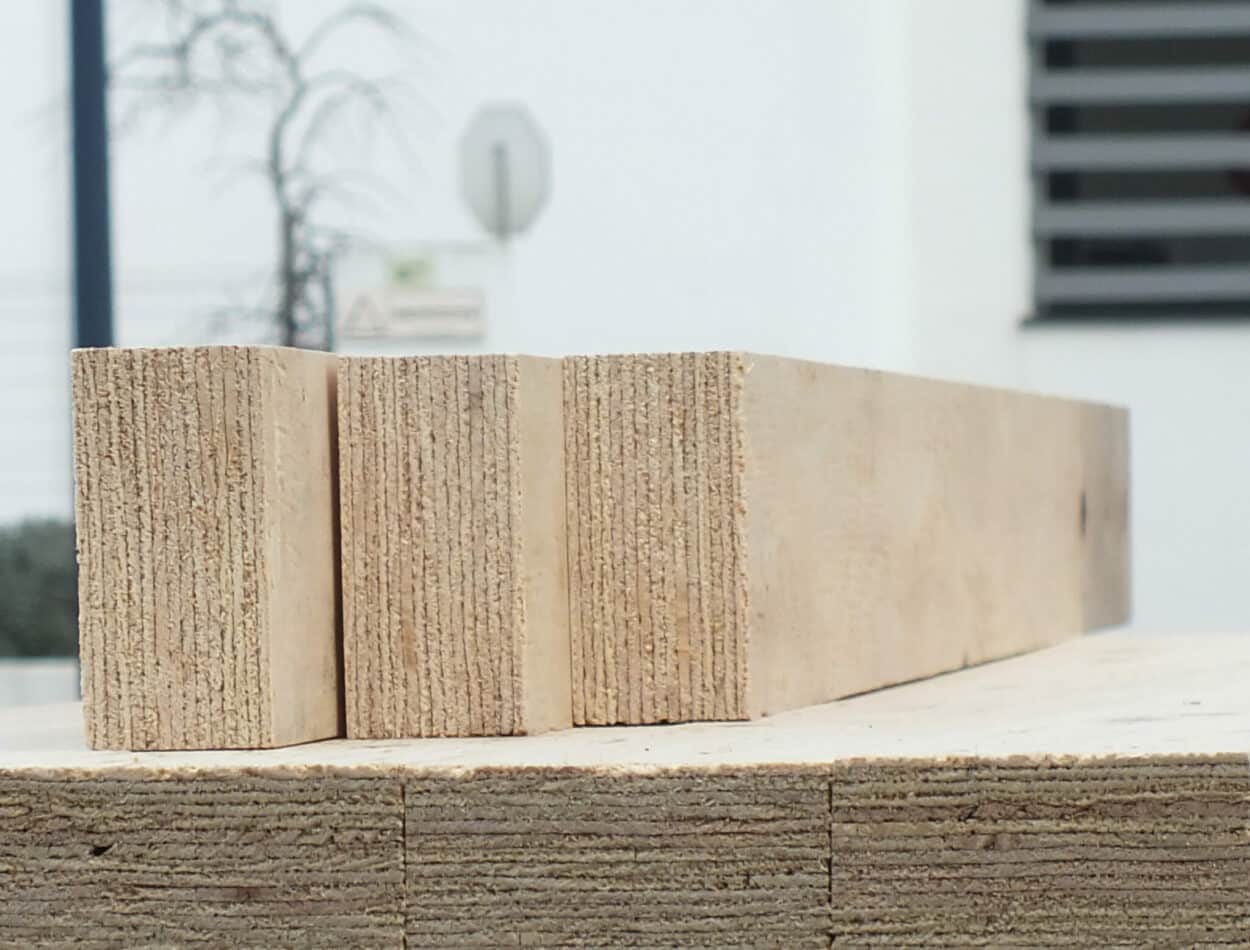