In an interview with BioBuildingBlock Founder Marco Citro, we discuss precise details about the company’s innovative bio-masonry bricks and BIO Panel, which utilize natural and recycled materials. The startup has 4 patents approved nationally and internationally in the green tech field. Its bricks are hitting the market now while the panels are to come.
This interview was conducted and written by ArchiExpo Content Managers Anne-Claire De Moro and Elena Nappi.
During Salone del Mobile 2024, we met Marco Citro, founder of BioBuildingBlock, a company based in Fisciano (Salerno, Italy) that is revolutionizing the building industry. Founded in 2020, the company aims to build environmentally friendly, sustainable, and safe buildings. BBB was awarded the International Innovation & Excellence Award by Corporate LiveWire in 2022, 2023, and 2024 as the best Italian innovative startup in the sustainability sector. The high innovative value of the startup BBB srl was also recently recognized with the “America Innovation Award” given by Fondazione Italia USA.
In our interview with Marco Citro, we learn more about the company’s products and the growing demand for modern housing that prioritizes human well-being and environmental preservation.
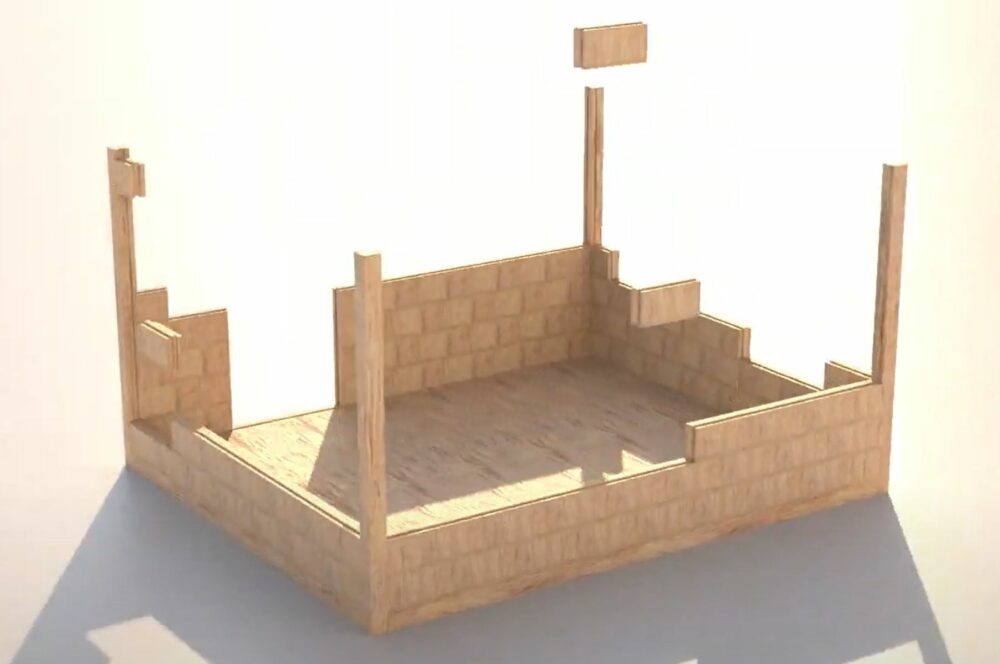
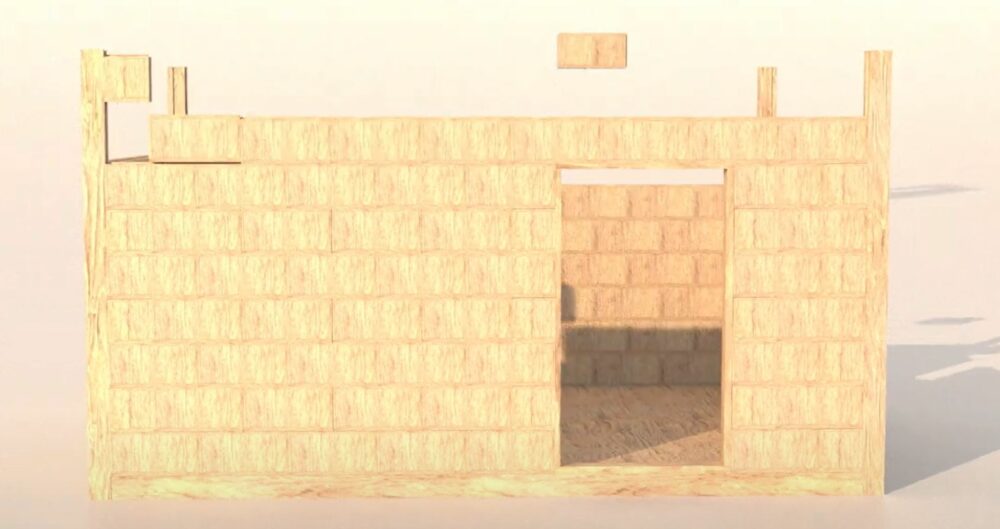
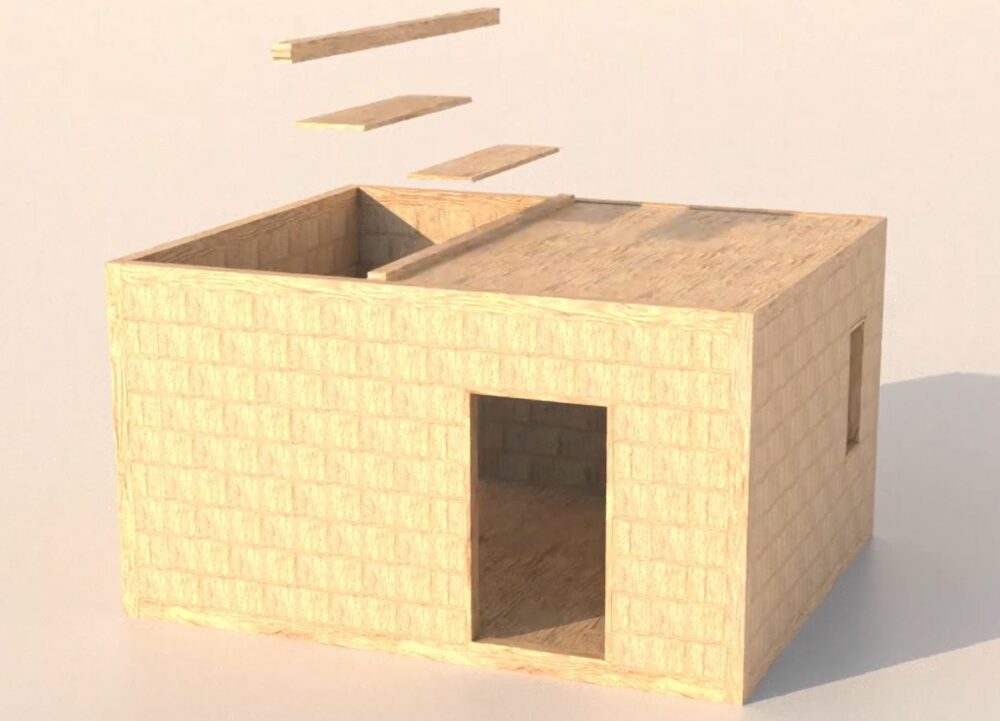
ArchiExpo e-Magazine: What are the main materials used in your products?
Marco Citro: We focus on the use of BFC- or FSC-certified natural materials, as in the case of our first product, covered by the International Patent, the bio-masonry, made with solid fir wood and steel bars that allow both vertical and horizontal joining of adjacent bricks. This allows the creation of real reinforced wood walls, providing greater resistance to natural events such as earthquakes, tornadoes, or hurricanes. We conducted technical tests in university laboratories to verify resistance to seismic events and strong winds, obtaining results comparable to winds of up to 300 km/h. The use of natural materials is essential to improve the acoustic and thermal insulation of bio-masonry, while also ensuring its breathability, which is essential for the well-being of inhabitants. The latter prevents the production of health-damaging substances called VOCs, or volatile organic compounds, thus helping to maintain healthy living conditions and prevent indoor pollution. Our goal is to provide maximum living comfort in terms of indoor quality.
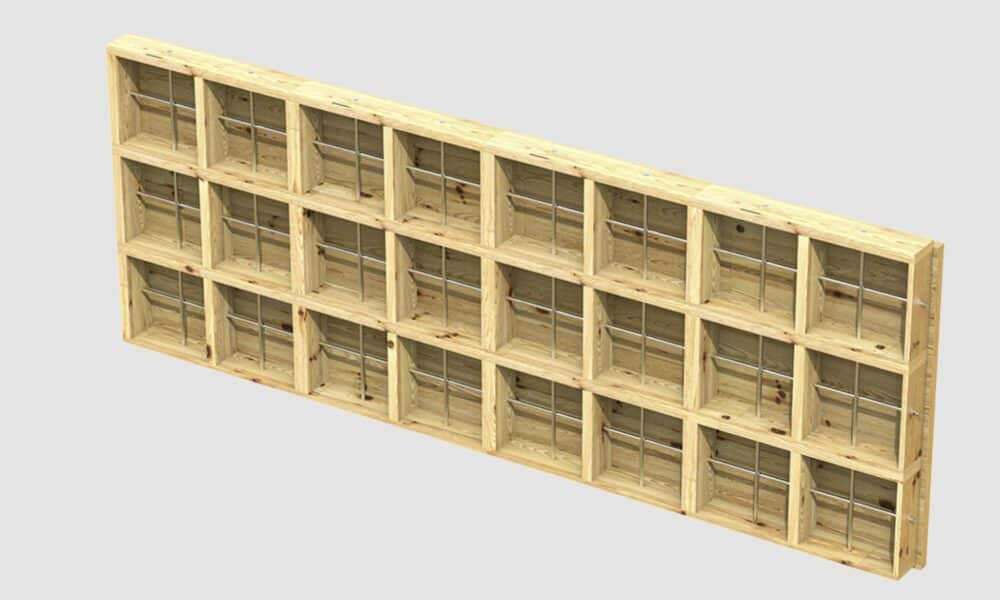
ArchiExpo e-Magazine: Do you propose other innovative products in the sustainable building sector?
Marco Citro: We also present BIO Panel, made from natural and recycled materials such as wood chips, cellulose obtained from recycled paper and cardboard, straw, hemp, and other plant fibers. We also use sheep’s wool obtained from recycling discarded clothing. Everything is held together by natural proteins of animal or plant origin, acting as glue instead of synthetic glue to compact the material and obtain the desired panel.
Again, attention is paid to breathability, fire, and water resistance. The proteins used are fire resistant, withstanding temperatures above 1000 degrees Celsius, and are hydrophobic. Regarding recyclability, the panel can be shredded and recycled at the end of its life cycle to produce new panels. Alternatively, it can be used as a soil conditioner, acting as a natural fertilizer.
ArchiExpo e-Magazine: Do your products generate zero waste during their life cycle?
Marco Citro: Certainly, our products are designed to eliminate waste during their life cycle. Our startup is committed to green tech, with these two specific products and others under development, always with an eye on the goals of the ONO 2030 agenda. This vision reflects our commitment to innovation, sustainability, and the circular economy, using zero-mile materials and maximizing the value of waste.
ArchiExpo e-Magazine: How does your company contribute to sustainability and emission reduction goals in construction, according to the European Green Deal?
Marco Citro: This European legislation requires new buildings to be zero-emission or Nearly zero-emission buildings (NZEB) by 2030. The BioBuildingBlock brick already makes it possible to achieve these parameters thanks to its high thermal insulation indexes. It is important to note that for both the brick and the panel, each kilogram of material—considering that the brick weighs 10 kilograms and the panel 1 kilogram—contributes to removing an equivalent weight of CO₂ from the environment. This, together with the use of renewable sources in production processes, ensures a strongly negative carbon footprint.
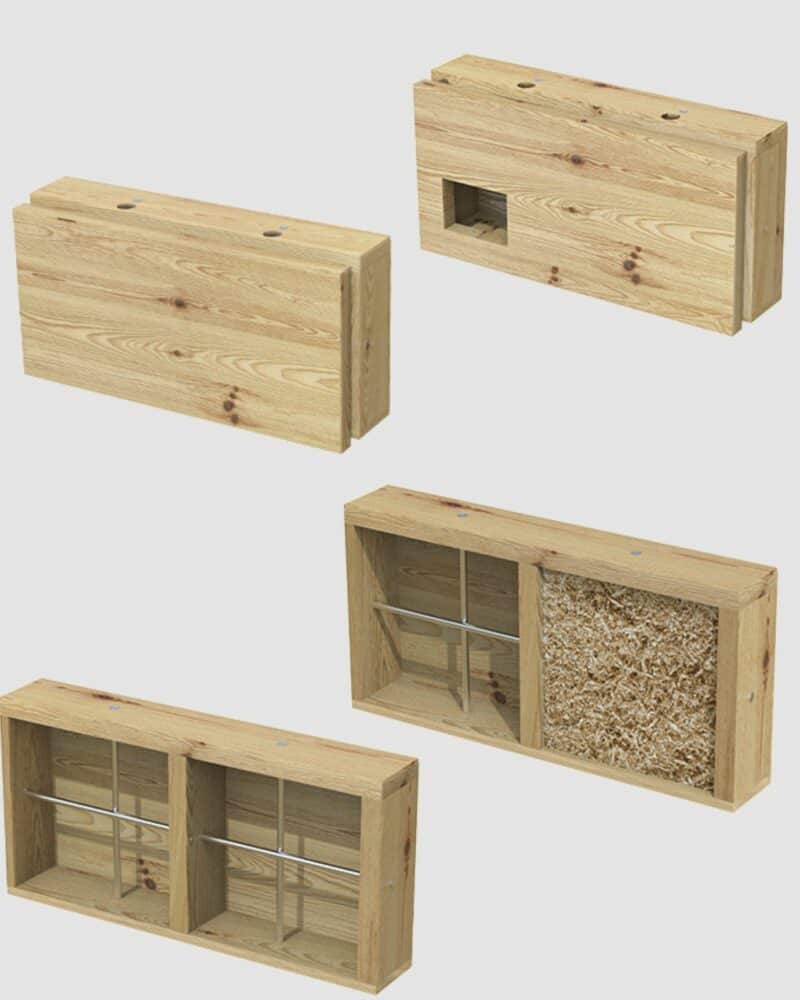
ArchiExpo e-Magazine: Do you also sell your products abroad?
Marco Citro: We are currently seeking collaborations with foreign countries to facilitate the startup’s international expansion. Therefore, we are not limiting ourselves to the domestic market but are aiming for the foreign market.
ArchiExpo e-Magazine: How do your bricks fit the specific needs of construction projects?
Marco Citro: Our bricks are easily assembled and versatile. In addition to the standard model, we offer variants with internal channels, which are useful for housing electrical installations or water connections. This not only simplifies design but reduces waste during assembly, thanks to our Lego-like system. With a team of four workers, it is possible to assemble the rough structure of a 100-square-meter house in just 24 hours, thanks to the quick connection between bricks. We follow technical standards by using a skeleton composed of wooden beams and pillars, complemented by our module to infill the walls.
ArchiExpo e-Magazine: Is it possible to construct multi-story buildings with your bricks?
Marco Citro: Our load-bearing brick, subjected to a series of experiments for certification, is capable of supporting very heavy loads, enabling the construction of even four- or five-story buildings. During the experimental tests, the compressive strength showed values corresponding to about 140 tons before breaking, representing an efficiency of 80 percent compared to concrete masonry. Our building system is much lighter than a reinforced concrete wall, weighing 6 or 7 times less, which also reduces the inertia force in case of an earthquake. The elasticity of both the wood and the internal steel lattice allows for greater dissipative capacity of seismic waves.
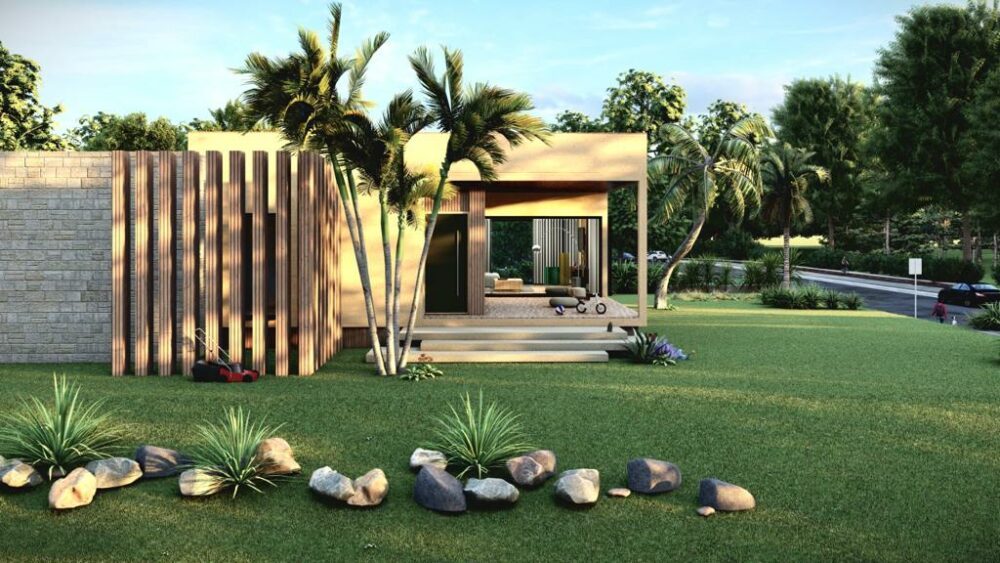
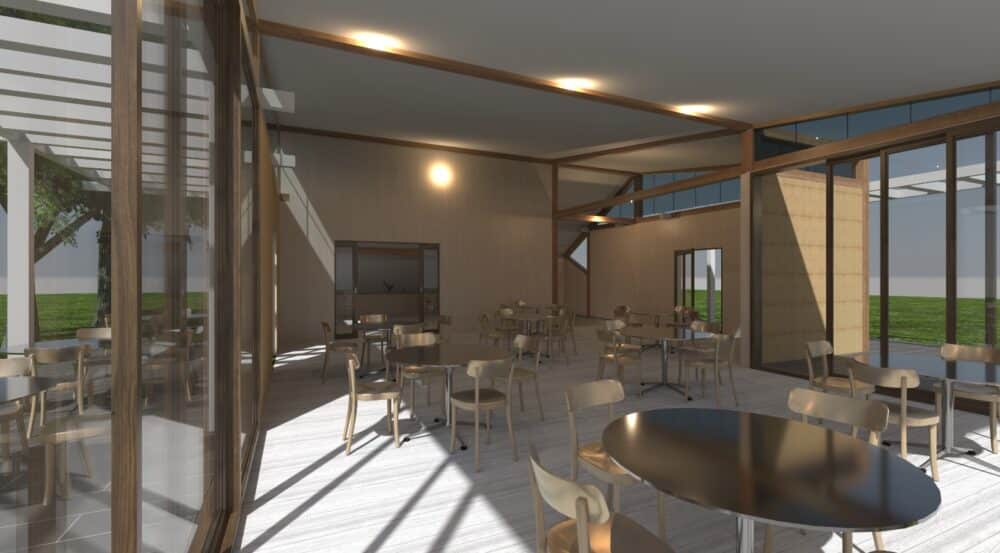
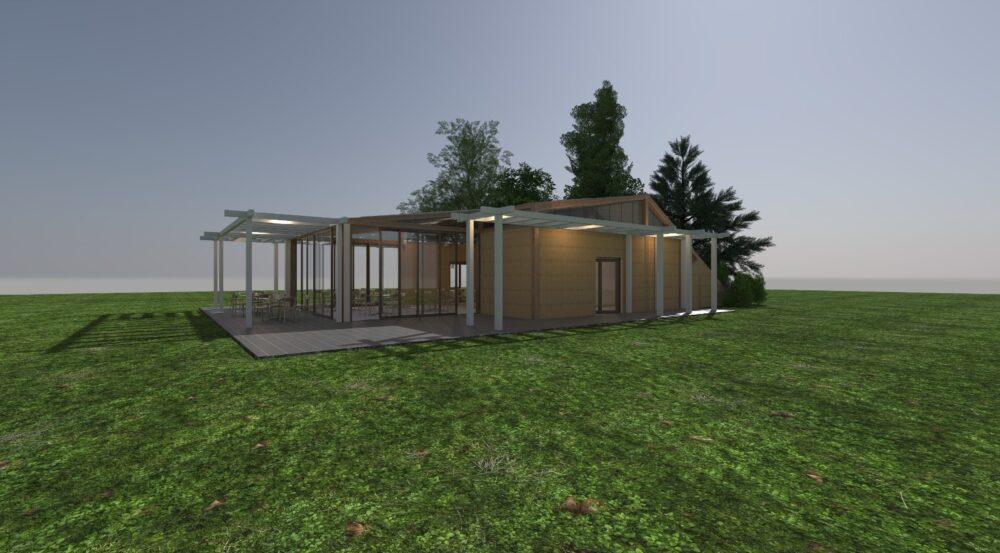
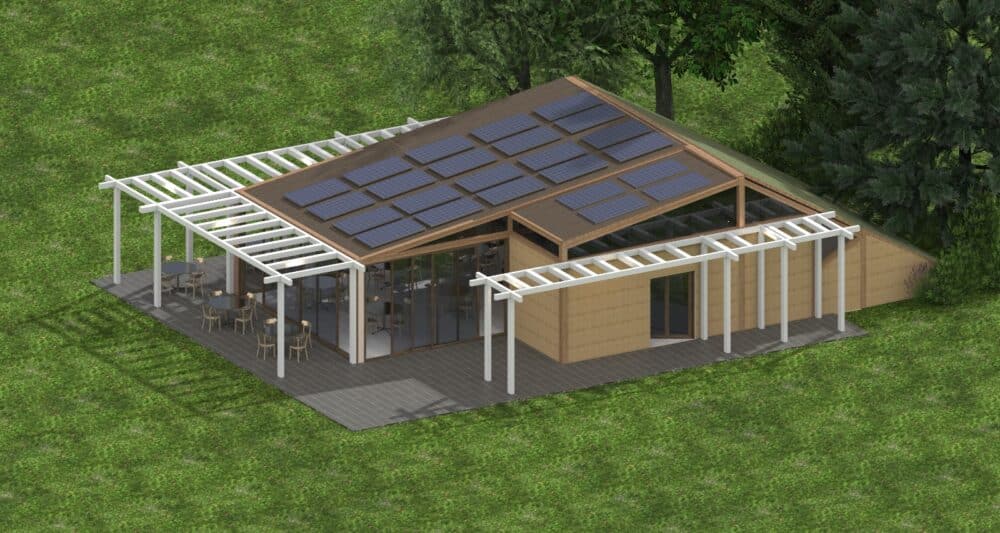