We catch the founder of French company ID Maison Bois to discuss the off-site manufacturing and cost optimization of these modular, timber-frame houses. The company has recently expanded its portfolio with office solutions and more.
In response to the housing crisis and environmental challenges, ID Maison Bois is revolutionizing the construction industry with an innovative concept: modular timber-frame houses delivered turnkey in only 72 hours. By leveraging off-site manufacturing and cost optimization, the Savoy-based company offers accessible solutions starting at €95,000 for a 60 m² home.
Despite the difficult economic climate, the French continue to dream of home ownership, and nearly 8 out of 10 renters would like to acquire a home, a cocoon adapted to their family life. ID Maison Bois responds to this aspiration with affordable, sustainable solutions. With over 1,000 completed projects, ID Maison Bois meets the evolving expectations of homebuyers by combining speed, energy efficiency, and compliance with RE 2020 standards.
Beyond individual homes, ID Maison Bois expands its offering with flexible solutions such as the Wooden Tipi, Garden Office, and Garden Studio, which can be installed without a building permit. These alternatives attract private buyers and professionals looking for adaptable living and working spaces. By focusing on sustainability, customization, and cost control, the company is positioning itself as a key player in France’s modular housing sector.
We spoke with Damien Roy, Managing Partner of ID Maison Bois, to learn more about the company’s structures.
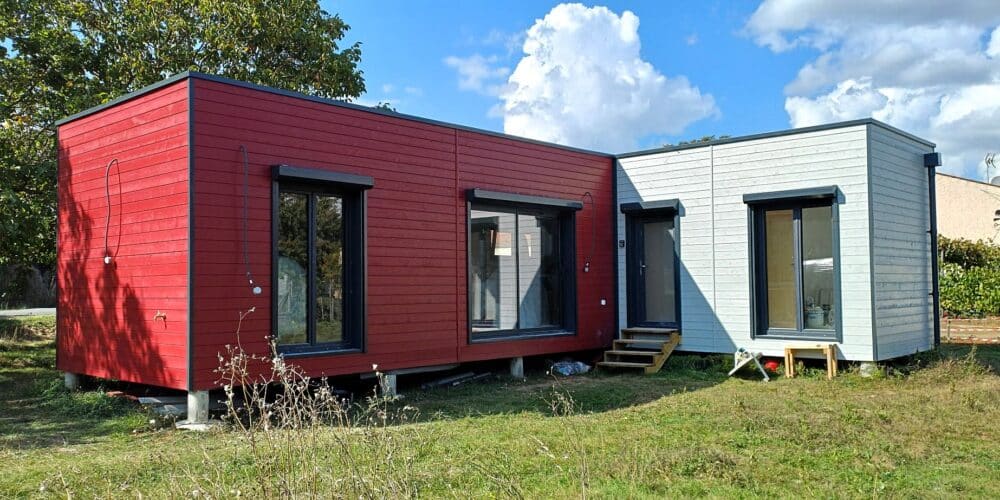
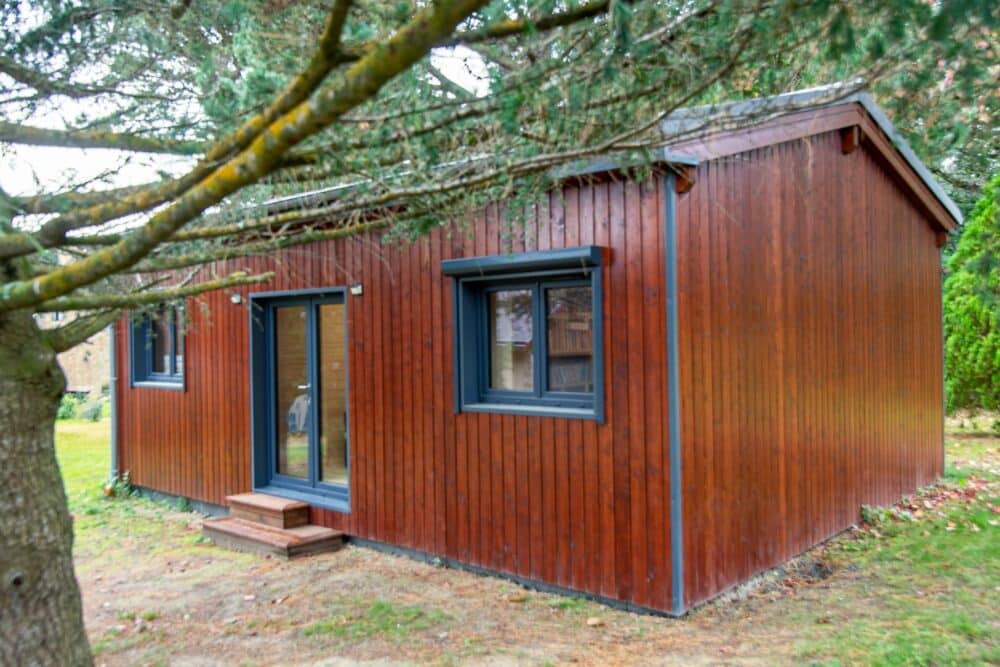
Challenges: The Housing Crisis, Off-site Construction, and RE 2020 standards
ArchiExpo e-Magazine: Can you give us some background information about the housing crisis?
Damien Roy: The housing crisis in France has existed for more than 20 years but has intensified in recent years due to several factors. Construction has slowed significantly, particularly in social housing, and there are long waiting lists in major cities. The cost of land has also increased due to scarcity, and the price of materials has risen sharply since the COVID-19 crisis and the war in Ukraine. Additionally, there is a growing shortage of skilled construction workers, making traditional construction slower and more expensive.
ID Maison Bois was created in 2004 and has managed to address some of these issues by offering an alternative approach through modular timber-frame houses. Initially, we acted as intermediaries before becoming full manufacturers, allowing us to control costs and quality.
ArchiExpo e-Magazine: What are the main technical challenges associated with off-site construction, and how do you overcome them?
Damien Roy: One major challenge is accessibility. We work with large cranes to deliver homes, and some sites are difficult to reach. Another challenge is transitioning from using a steel-based modular framework to a fully wooden structure. We are currently exploring ways to replace steel with wood while maintaining structural integrity. Additionally, off-site production requires precise planning to ensure that all elements fit perfectly during on-site assembly.
ArchiExpo e-Magazine: How do you ensure that your modular homes meet RE 2020 standards while optimizing costs?
Damien Roy: Our homes are built using a dry construction process, which significantly reduces environmental impact. We use micro-piles or small concrete foundations instead of large concrete slabs, preserving biodiversity and reducing material consumption. The structures themselves are primarily made from wood, a renewable resource, and we use sustainable insulation materials like wood fiber and mineral wool. By manufacturing in a controlled environment, we minimize waste and improve efficiency.
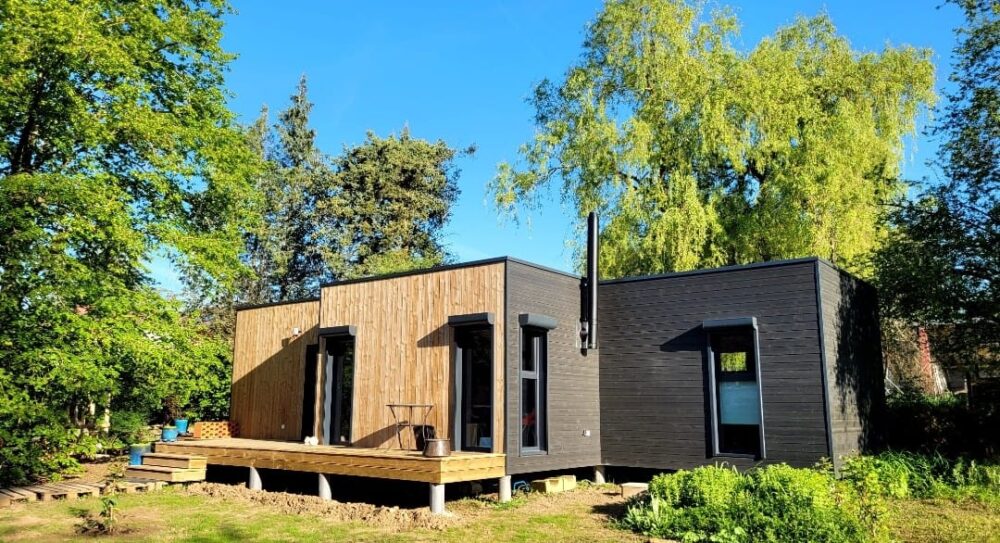
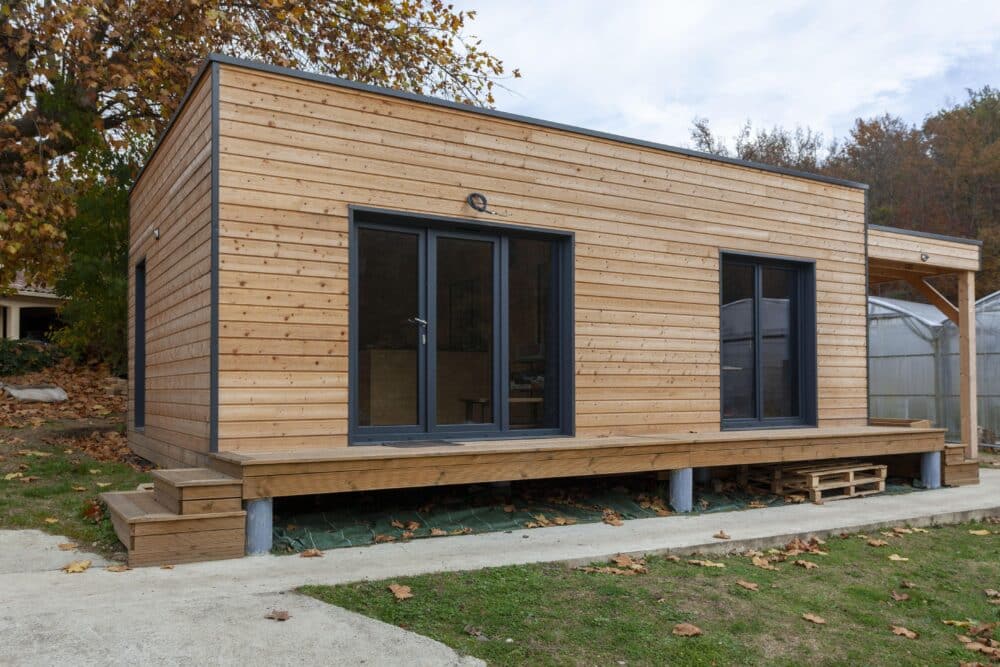
Modular Homes: Lifespan, Bio-sourced Materials, and Speed
ArchiExpo e-Magazine: What is the average lifespan of a timber-frame house, and how does it compare with traditional construction?
Damien Roy: A well-constructed timber-frame house has the same lifespan as a traditional concrete house, typically 50-60 years or more, provided it is well maintained. Some timber buildings in Europe and Japan have lasted for centuries. Maintenance over time may include reinforcing insulation or replacing external elements, but the core structure remains solid.
ArchiExpo e-Magazine: Can you describe the bio-sourced materials you use and their impact on the carbon footprint of your buildings?
Damien Roy: Approximately 80-85% of our buildings’ materials are bio-sourced. We use solid wood for the structure, wood-based insulation, and wooden interior finishes instead of plasterboard. Our external cladding is treated and painted in our facilities using water-based paints. We work with an Austrian supplier that ensures our materials are sustainably sourced. By avoiding high-carbon materials like traditional concrete and steel, we significantly lower our homes’ carbon footprint.
ArchiExpo e-Magazine: How does your off-site production model affect the quality and speed of project delivery?
Damien Roy: Off-site production allows us to build in a controlled environment, avoiding weather delays and ensuring high precision. It also reduces waste and optimizes material use. Since everything is pre-assembled in the factory, on-site work is minimized, enabling us to deliver a turnkey home within 72 hours of site preparation.
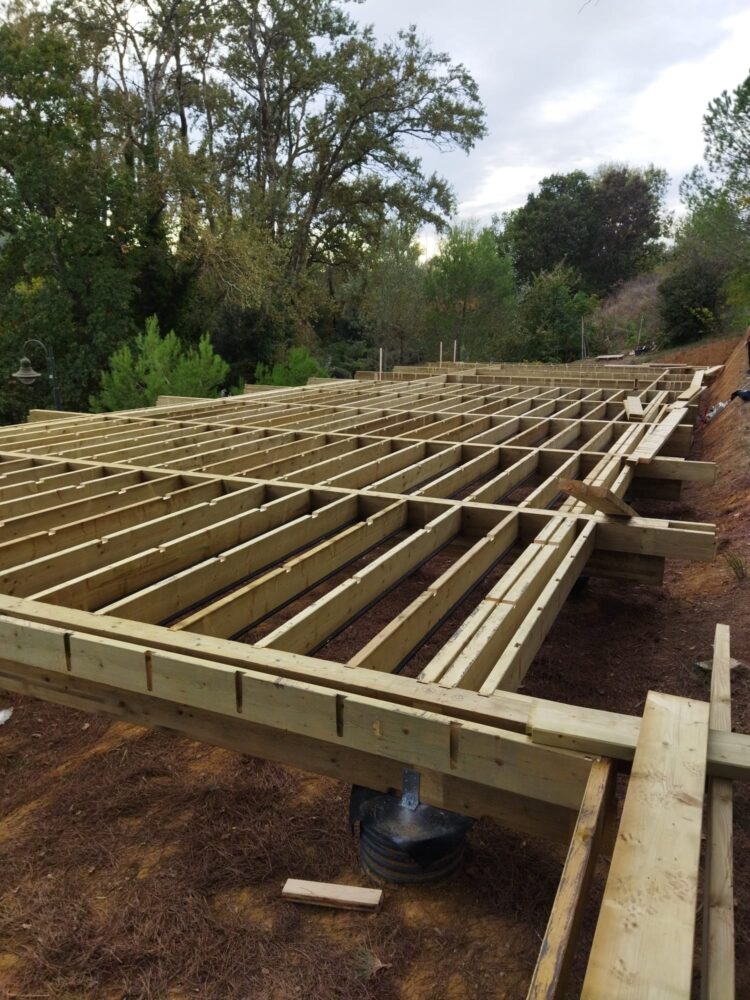
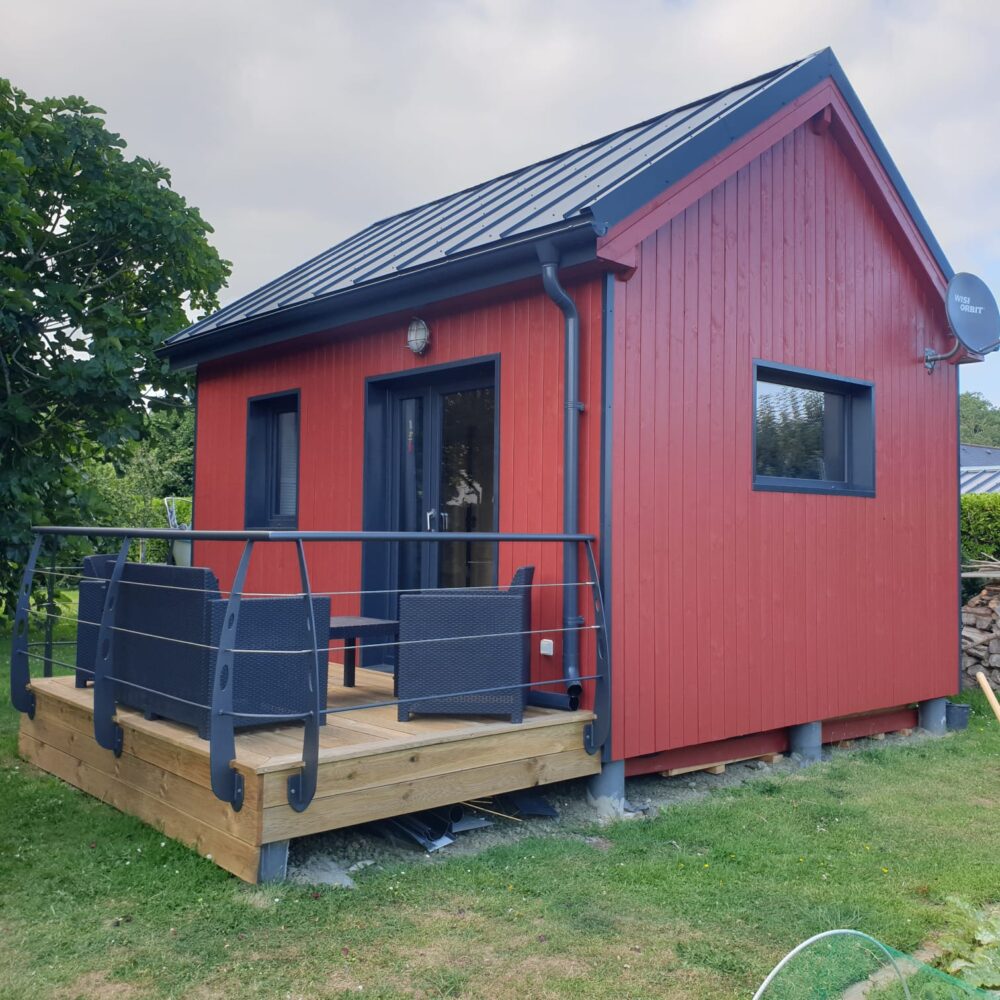
Regulatory Levers and Innovations
ArchiExpo e-Magazine: What regulatory and administrative levers have you put in place to facilitate homeownership for your customers?
Damien Roy: We design homes that comply with local building regulations and assist clients with administrative procedures. Some of our smaller models, such as the Garden Office and Garden Studio, do not require building permits, making them attractive options for quick installation. We also offer financing solutions through partnerships to make homeownership more accessible.
ArchiExpo e-Magazine: How do you plan to expand your range or incorporate innovations in modular housing?
Damien Roy: We continue to develop new solutions, such as small-scale collective housing projects using modular timber-frame construction. We recently completed a project for seven accessible studio apartments for disabled individuals in Angers. Additionally, we are exploring new insulation techniques and construction methods to improve energy efficiency and affordability. We remain focused on our core market—compact, high-quality, sustainable homes—but we are also adapting to emerging needs in the housing sector.