The World of Modular event emphasizes the transformative potential of modular construction in addressing the US housing crisis, and looks forward to the industry’s next milestone event in Brussels, Belgium, on October 1-2, 2024.
March 18-21, 2024—The Modular Building Institute (MBI)’s 41st Annual Convention & Tradeshow, held in Orlando, Florida, marked another successful gathering for professionals in the commercial modular building industry. Following an attendance growth average of nearly 25% over the past three years, the World of Modular event drew nearly 1,500 individuals from across the modular construction industry and around the globe. Against the backdrop of a persistent housing crisis in the USA, the event underscored the pivotal role of modular construction as a viable solution to meet the escalating demand for housing and infrastructure.
“Construction stares right at time and money,” Matt Laase, principal of Jackson Main Architecture, stated during the Building Hope in a Housing Crisis conference. “So how do we build hope in a housing crisis? Maybe you don’t fully know until you’re a little bit more involved.”
Time and money, zoning regulations and a shortage of construction workers; the housing crisis sits on a multi-layered foundation of issues. While modular construction offers potential time and cost savings, with project completion times up to 50% faster than traditional methods and reduced material waste due to controlled factory processes, the industry continues to face challenges in sourcing skilled labor. Also, a study by the Modular Building Institute found that modular construction reduces site disturbance by up to 90% compared to traditional construction methods, as restated in an article published by Northgate Modular on LinkedIn.
During our tour of the World of Modular event, we identified a few transformative potentials of modular construction in addressing the pressing challenges of housing affordability and infrastructure development.
Secure and Sustainable Housing Options for Communities Facing Environmental Risks
Elevated Modular Systems presented a pioneering approach to address the critical issue of housing affordability and infrastructure development by offering unparalleled protection against flooding and storm damage. Engineered with robust structural steel modular foundations, including full H-beam support and deep-set footings, this innovative solution ensures unmatched strength and durability, safeguarding modular and mobile homes even in the face of severe weather events. By raising homes 8-12 feet above ground level, Elevated Modular Systems not only exceed FEMA flood stage requirements but also ingeniously utilize the space beneath the structure, transforming it into functional areas for elevated living.
“We’re trying to come up with ideas to prevent houses near the beaches from being destroyed in the future,” Britt Smith, Sales Associate at Elevated Modular Systems LLC., said. “The steel is what’s gonna make the houses more durable.”
Beyond fortifying homes against the threat of high water, this patent-pending system significantly reduces insurance costs associated with flood damage, making it an indispensable choice for residences situated in flood-prone regions. By offering robust cost-effective structural steel modular foundations that raise homes above FEMA flood stages, the system mitigates the risk of flood damage, which is a significant concern for many homeowners, particularly in vulnerable regions. This protection is crucial for preserving housing stock and preventing displacement, especially in areas where flooding is a recurring issue. Additionally, by reducing insurance costs associated with flood damage, Elevated Modular Systems makes homeownership more financially viable and accessible, thus contributing to efforts to alleviate the affordability challenges within the housing market.
The Elevated Modular Systems solution aims to strengthen the durability and longevity of housing structures in flood-prone areas while helping to address one aspect of the broader housing crisis: providing secure and sustainable housing options for communities facing environmental risks.
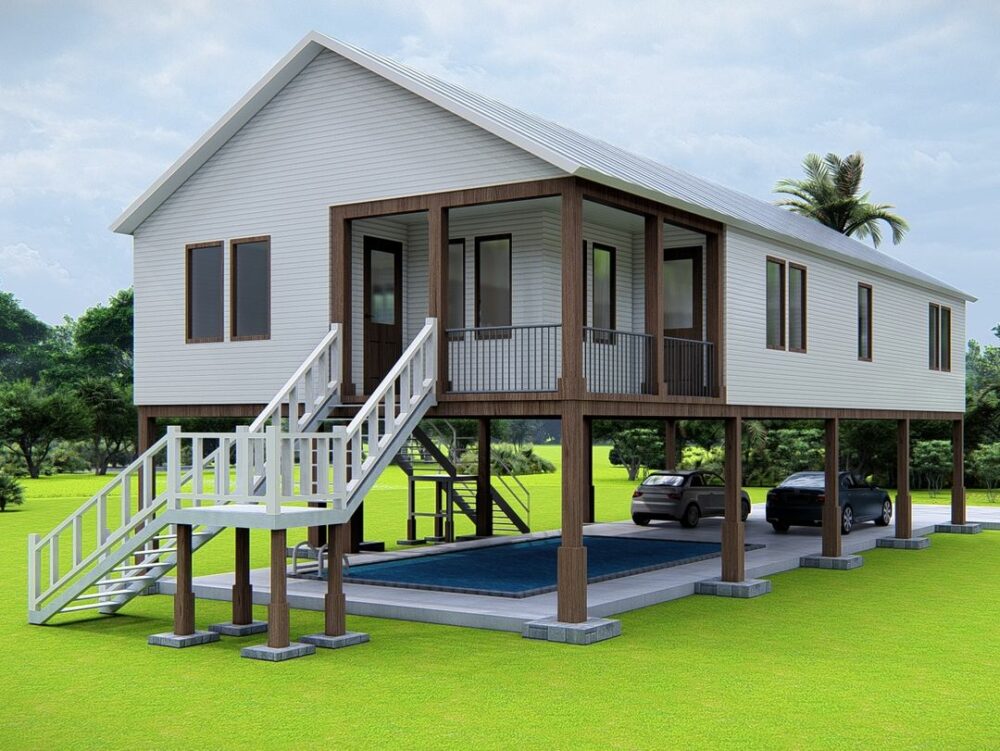
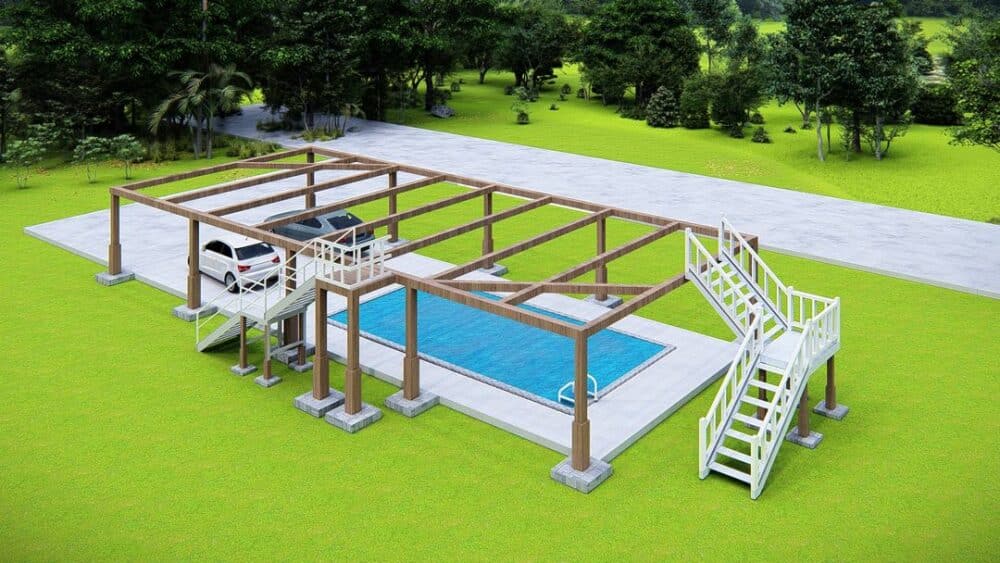
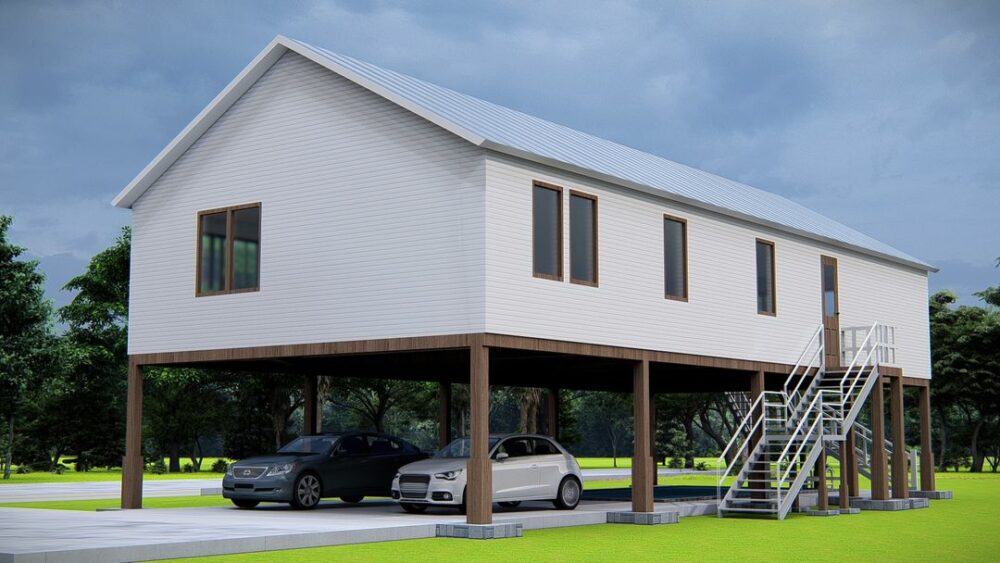
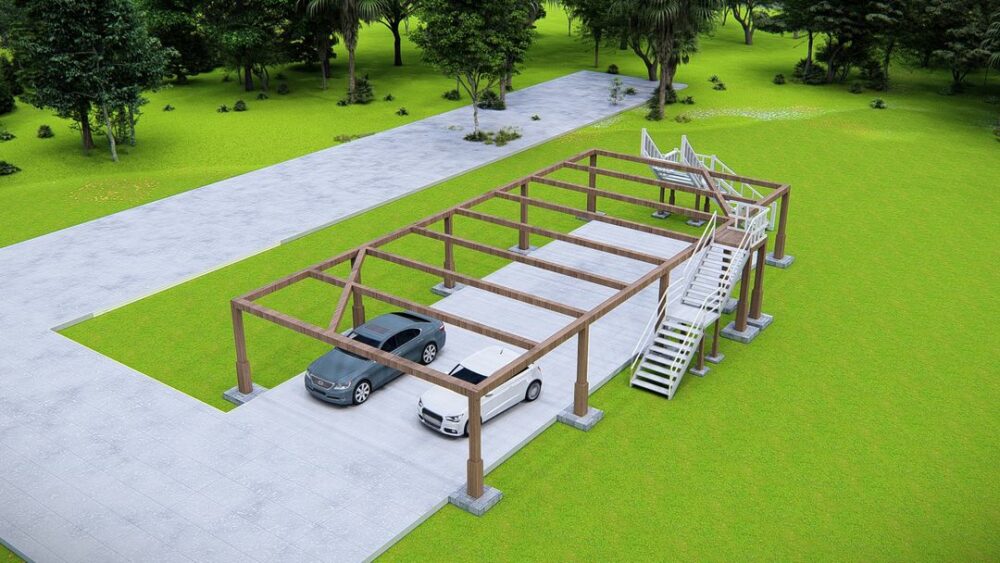
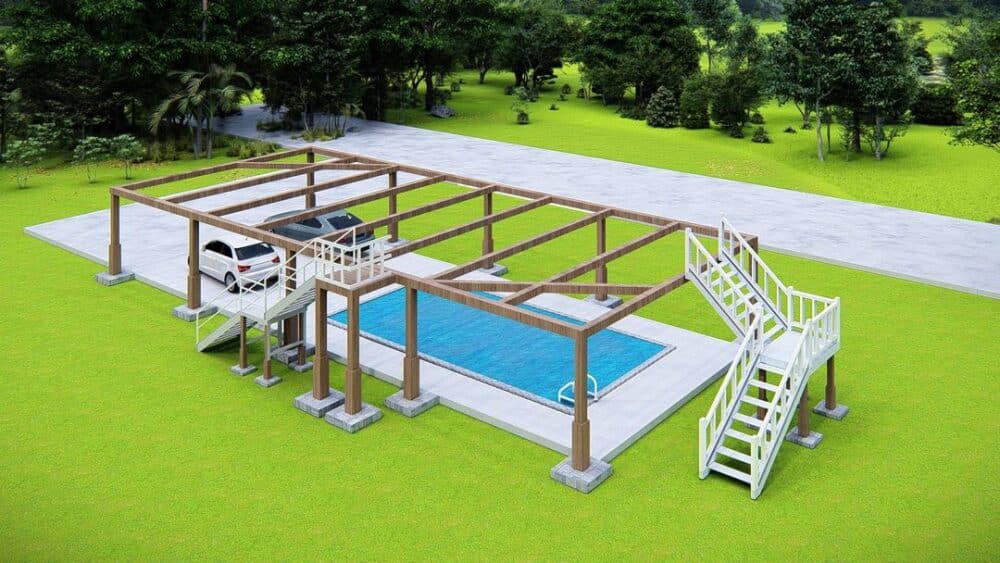
Digitalizing Speed: BIM for Prefab Construction
In Europe, Estonia stands out for its extensive expertise in modular housing and tiny home construction. With a rich history in prefabricated housing, Estonian manufacturers now produce a diverse array of high-quality, energy-efficient homes customizable to individual needs. Leveraging modular construction techniques, these manufacturers can swiftly assemble homes on-site within weeks. Companies like Build.works capitalize on this expertise by integrating digital technologies to further expedite the construction process. Build.works offers a specialized software-as-a-service (SaaS) platform tailored for prefab construction, facilitating sales, budgeting, scheduling, offsite production, and construction management to enable engineer-to-order (ETO) production scenarios.
A key feature of build.works is its intuitive interface, facilitating seamless collaboration, progress tracking, and project management for construction professionals across locations and time zones. By providing real-time insights and data analytics, build.works empowers prefab production and construction companies to make informed decisions and streamline their operations. At the World of Modular event, Peeter Pärna, founder and CEO of Build.works, highlighted the platform’s accessibility, emphasizing its usability for professionals regardless of experience level.
“It doesn’t matter if you have 30 or 10 years of experience. it all depends on your way of thinking.”
Earlier this year, build.works announced its collaboration with SAP Industry Cloud, a leading Software as a Service (SaaS) solution. This partnership marks a significant milestone in prefab and construction management, promising enhanced efficiency, scalability, and innovation. By merging the strengths of Build.works’ advanced SaaS platform with SAP’s industry-leading expertise and resources, the collaboration aims to revolutionize construction management. Through improved integration, scalability, data-driven insights, and global reach, construction companies can expect heightened efficiency and project success.
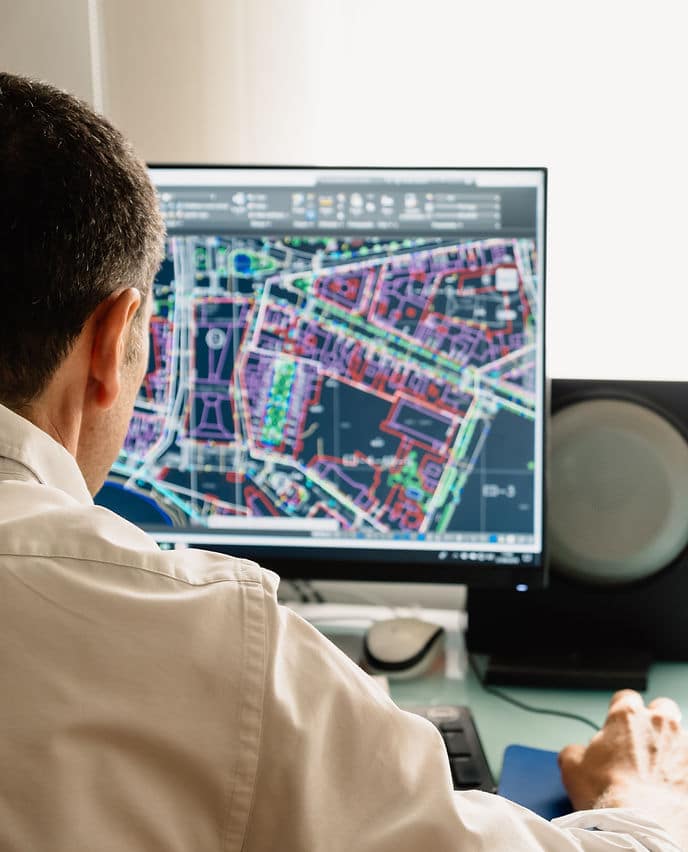
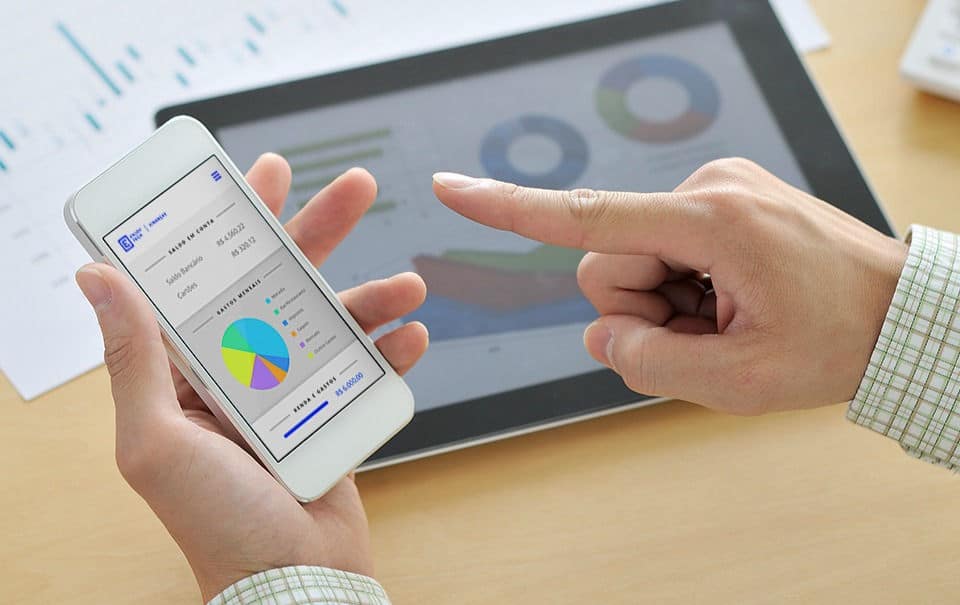
VBC, a Growing Leader in Modular Construction for Affordable Housing
Volumetric Building Companies (VBC) made a significant impact at the conferences, showcasing its innovative approach to modular construction across continents. With strategically located factories in California, Pennsylvania, and Poland, VBC has emerged as a leading player in the modular construction industry, renowned for its dedication to quality and efficiency. Founded in 2009 with headquarters in Philadelphia, VBC experienced substantial growth with strategic acquisitions and partnerships while maintaining its objective to create affordable housing.
In 2021, VBC acquired the assets of the California-based modular tech firm Katerra, marking a significant expansion of its manufacturing capabilities and operational footprint. The following year, VBC merged with Poland-based manufacturer Polcom, amplifying its global presence and bolstering its expertise in modular construction. These strategic moves empowered VBC to offer comprehensive solutions for large-scale projects while maintaining its commitment to quality and efficiency. Operating within over 1.25 million square feet of manufacturing space across multiple continents, VBC continues to lead the way in delivering innovative modular construction solutions to meet the evolving needs of communities worldwide.
A core focus for VBC has been addressing the urgent need for affordable housing in the United States. Roughly half of VBC’s modular production is allocated to affordable multifamily housing, with an additional percentage designated for market-rate multifamily housing and hotels. This commitment to providing housing solutions aligns with the company’s mission to bridge the gap between household formation and new-home construction, particularly in regions facing chronic housing shortages. VBC’s innovative approach enables projects to be completed twice as fast as traditional methods, with greater budgeting certainty. Vice President of Design, Sara-Ann Logan, underscores VBC’s commitment to attracting a diverse workforce, including young women, by leveraging modern technologies and traditional construction methods such as fishbone flow. These methods ensure dimensional accuracy and contribute to significant savings in materials, energy, and construction costs.
“We’re not building a rocket to go into space here, right?” Logan said. “Our methods are practical and accessible so you can have someone on the manufacturing line who [can progress quickly and gain additional skills.]”
Moving forward, Volumetric Building Companies remains dedicated to driving innovation and sustainability in the construction industry while delivering high-quality modular solutions to meet the evolving needs of communities worldwide.
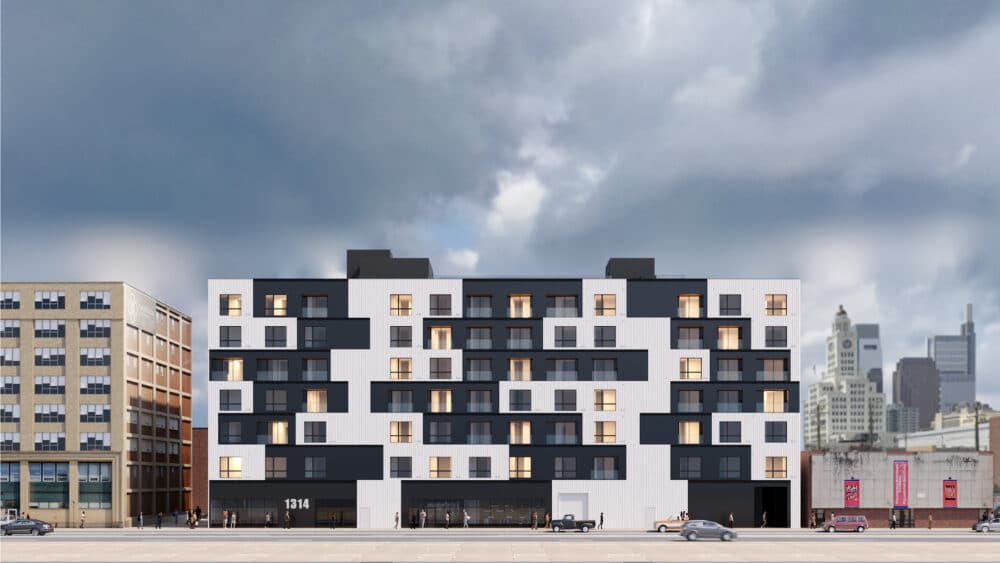
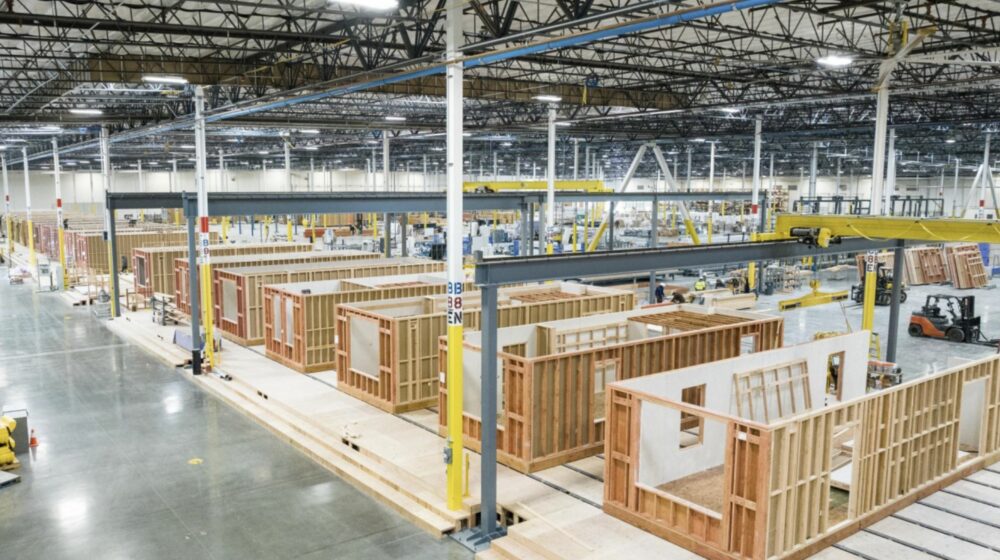