In a webinar hosted by Zen Modular, architecture professionals discuss how hybrids might make more sense—combining traditional, modular, and 3D-printed construction methods.
On February 13, Zen Modular held an online discussion with industry professionals on how the world of modular is transforming construction practices. During the Zen Talk, entitled “Modular construction / Architecture: First designs & feedback”, guest speakers responded to multiple questions regarding budget, standardization, collaboration, and durability.
As a digital platform, Zen Modular curated this series of webinars to allow architects to share their experiences with modular concepts. This integrated marketplace enables builders and architects to construct buildings from modules manufactured by a network of certified manufacturers. On the road to democratizing modular construction, the French company aims to transform the building industry through an Object-Oriented Construction approach.
The panel consisted of Pascal Chazal, CEO of Zen Modular, Nicolas Ziesel (KOZ Architectes), Vincent Ballion (Bellecour Architectes), Claude Brugière (Architecte spécialiste santé) and Emmanuel Coste (Agence Coste Architecture), each sharing their perspectives on the sector.
Modular Construction and Its Perception in Architecture
For many architects, modular construction has long been perceived as a temporary or low-quality solution.
“The notion of modularity often makes architects uneasy,” Claude Brugière noted. “We tend to associate it with uninspiring, short-term structures like construction site barracks or emergency hospitals.”
However, the panelists emphasized that modern modular methods have evolved far beyond these stereotypes. Today, modular elements are integrated into high-end, durable projects, proving that prefabrication can be a viable architectural tool rather than a constraint. Brugière shared an example of a successful hybrid modular project:
“The Jakarta Hotel in Amsterdam is a prime illustration of how we can blend traditional and modular techniques. The lower structure was built conventionally, while the upper floors used prefabricated modules, allowing for rapid assembly on-site.”
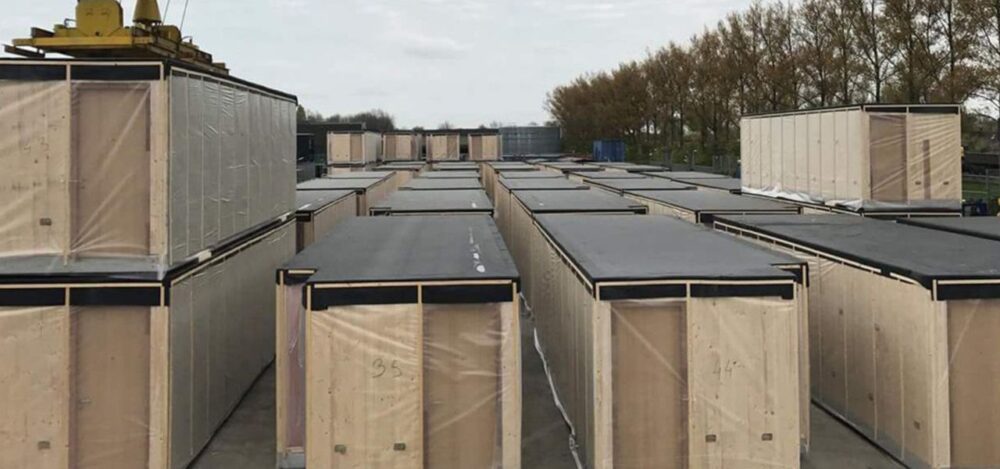
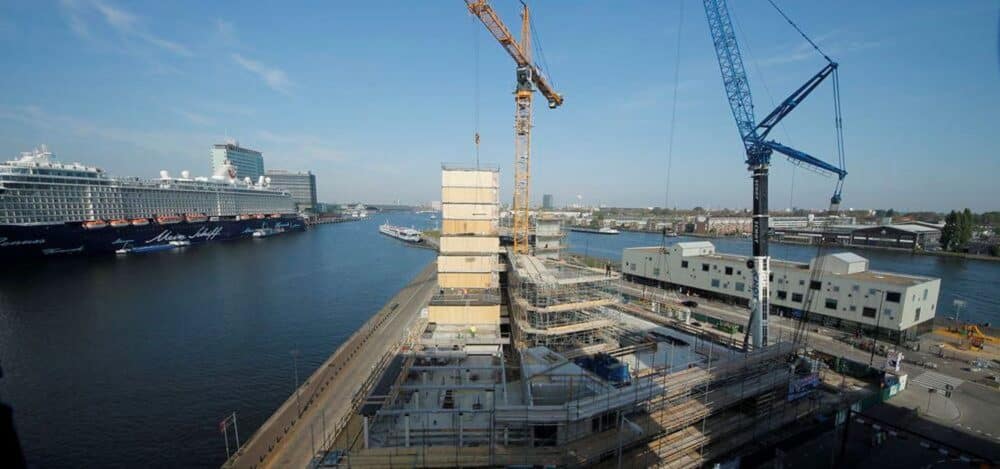
Integrating the modular concept into the construction and design of buildings is fitting for any sector, from luxury to healthcare. Brugière described how he has working on modular approaches for elder care facilities (EHPAD).
“We have moved beyond the prototype stage, creating flexible, well-designed modules specifically for senior housing,” he explained. “The focus is on comfort, accessibility, and long-term durability.”
Emmanuel Coste reinforced this shift in perception, stating:
“What we see today is a complete redefinition of modular construction. It’s no longer about limitations but about possibilities. The ability to combine modular, traditional, and even 3D-printed elements allows for an unprecedented level of flexibility in design.”
Standardization vs. Creativity in Modular Construction
A key concern for architects is whether standardization limits creative freedom. Emmanuel Coste tackled this issue directly:
“At first, we made the mistake of thinking we had to do everything with modules, but that’s not the goal. The real challenge is knowing what should be modular and what should remain traditional.”
The discussion highlighted how modularity doesn’t have to stifle creativity but can actually enhance it when used strategically. Vincent Ballion emphasized the importance of hybrid approaches:
“We should view modular components as a toolkit rather than a restriction. It’s about identifying the repetitive elements—hotel rooms, student housing units, hospital rooms—and making those modular while still allowing for architectural expression in the overall design.”
The collaboration between architects and manufacturers is essential to maintaining this balance.
“We are not just ordering prefabricated boxes like cars,” Ballion said. “We are part of a design process that integrates industrial efficiency with architectural intent.”
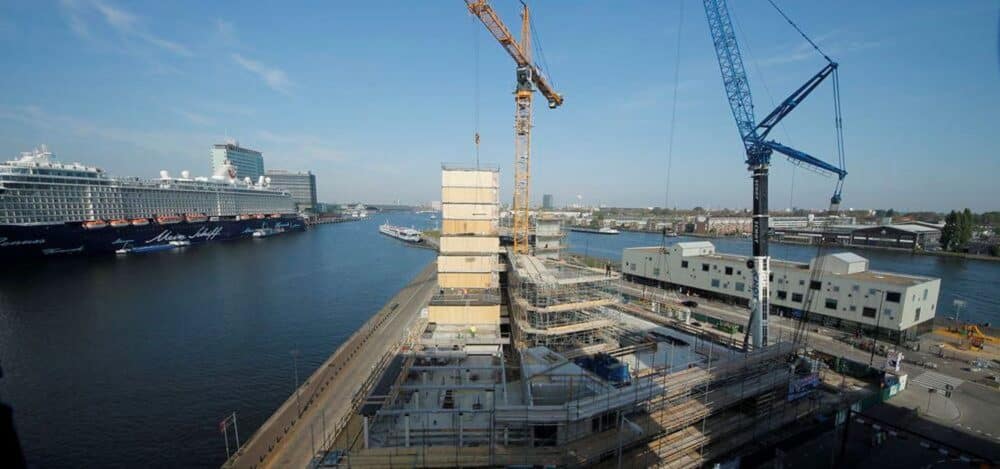
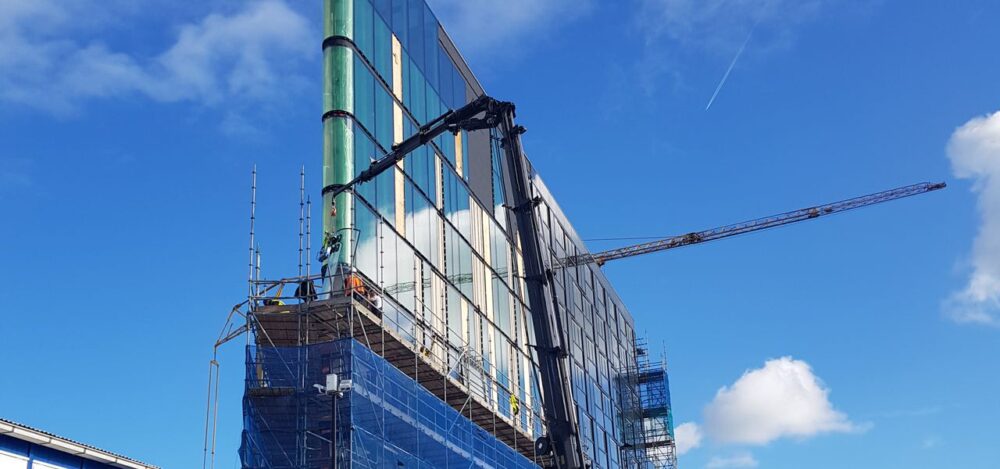
View modular components as a toolkit rather than a restriction.
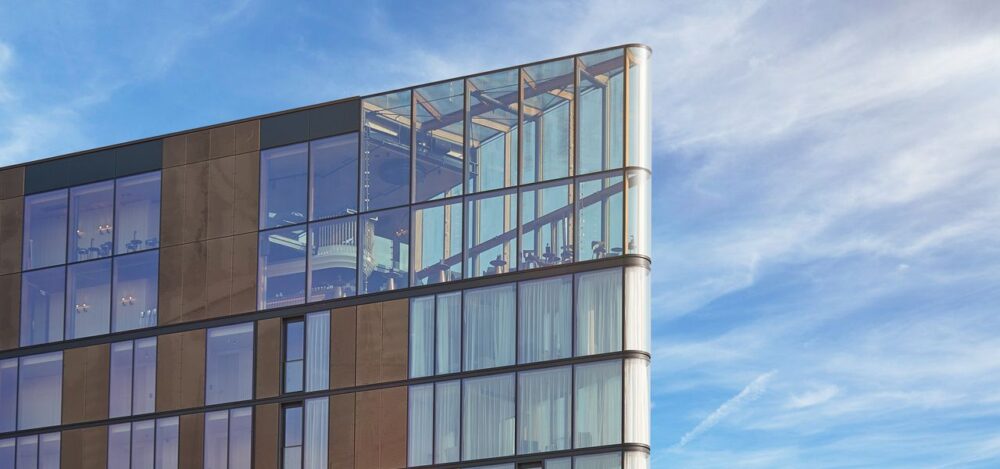
The Impact of Modular Construction on Costs, Timelines, and Sustainability
Beyond aesthetics, the speakers explored the concrete benefits of modular construction in terms of cost, speed, and sustainability.
“A fully modular project may not always be cheaper upfront, but the time savings are significant—reducing construction schedules by up to a year in some cases,” Emmanuel Coste.
Another key advantage is sustainability.
“Industrialized modular construction reduces waste and allows us to use materials more efficiently,” said Nicolas Ziesel. “With modules, we know exactly what we need before production begins, minimizing excess.”
However, modular construction is not necessarily the lowest-cost option in the short term.
“We are currently about 5-6% more expensive than traditional methods, but the reduced construction time, improved carbon footprint, and higher quality control in factories compensate for this,” Pascal Chazal.
Speakers also addressed concerns about modular buildings being too rigid in their designs.
“It’s not just stacking boxes,” Ballion clarified. “It’s about integrating modular efficiencies where they make sense while keeping the rest of the project adaptable.”
Integrate modular efficiencies where they make sense.
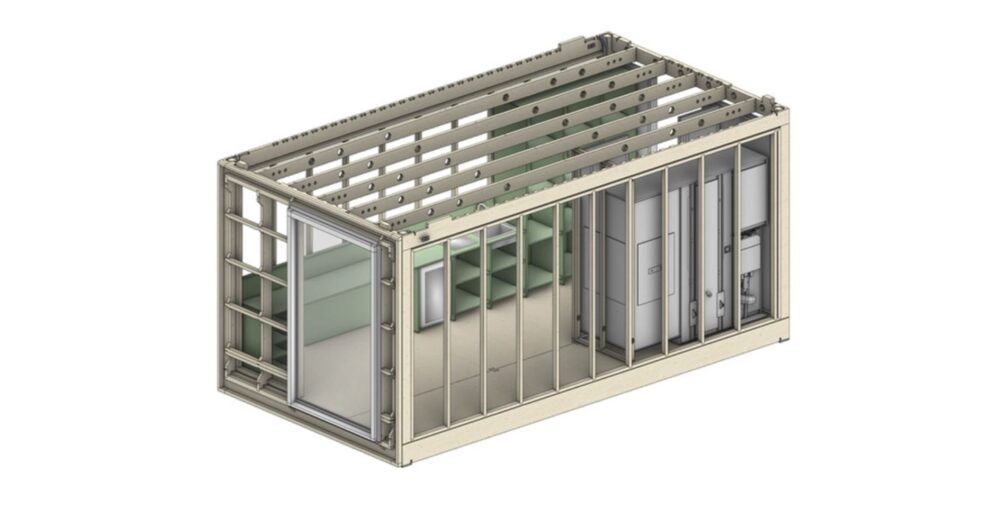
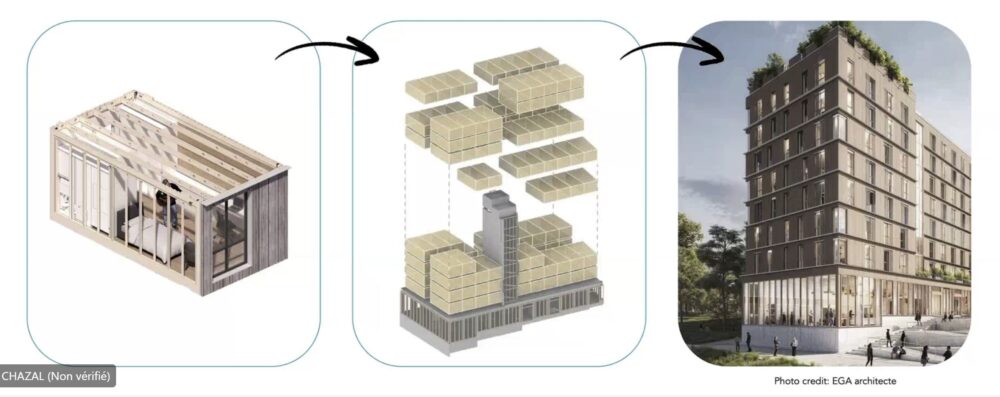
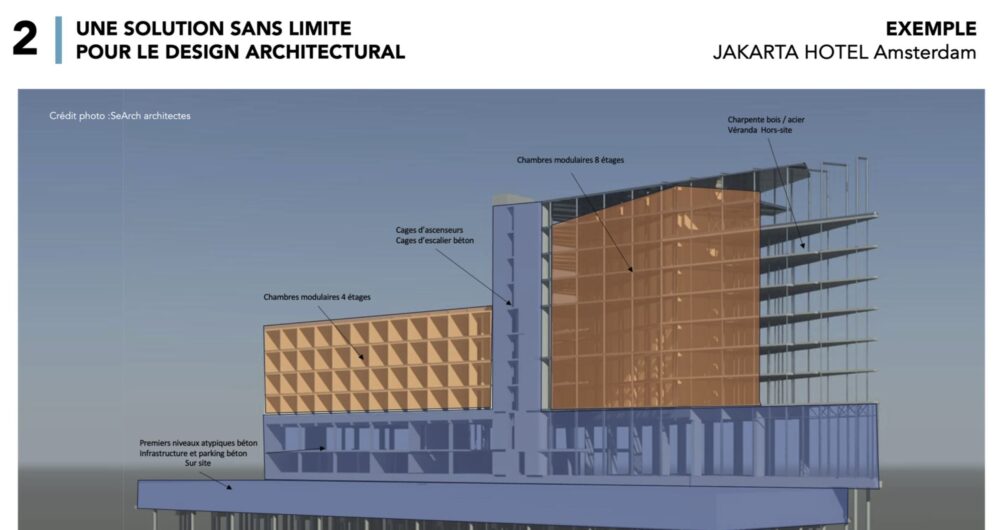
Ultimately, the discussion underscored that hybrid construction methods—a mix of traditional, modular, and even 3D printing—may be the best way forward.
“The future is in hybrid solutions,” Coste concluded. “By combining the strengths of modular, prefabricated elements, and conventional techniques, we can achieve better, faster, and more sustainable buildings.”
“3D printing is an incredible tool when used in the right context,” Coste continued. “We’ve learned that trying to build an entire structure with 3D printing isn’t always feasible, but using it for specific structural elements—such as walls or unique design features—can be highly effective.”
One notable example discussed was a housing project in Reims, which combined 3D-printed walls with prefabricated modular components.
“Instead of forcing a single method onto the entire project, we identified where 3D printing made sense and where prefabrication was the better choice,” Ballion noted. “The result was an efficient and visually striking design.”
Looking forward, the panelists agreed that hybrid construction—including modular, traditional, and 3D-printed elements—offers the most promising future for the industry.
“We are at the beginning of a new era in construction,” Coste concluded. “By integrating these technologies intelligently, we can create buildings that are faster to build, more sustainable, and more architecturally exciting.”